Do Ammonia Crackers make sense?
Several companies have announced plans to build ammonia crackers to use ammonia as a hydrogen carrier. However, do they make sense as long as existing ammonia facilities run on fossil-based hydrogen?
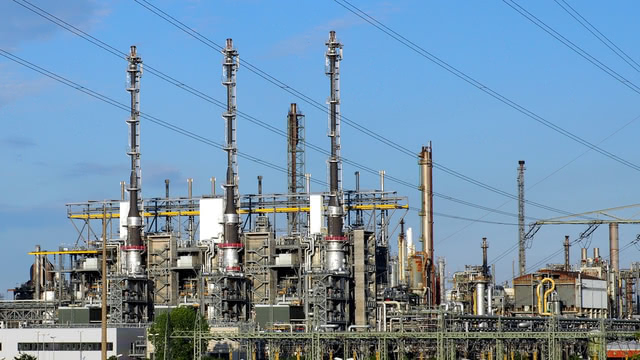
Hydrogen is a promising option to reduce emissions in sectors like steelmaking or the chemical industry where the direct use of electricity is difficult or impossible. Many countries in Europe with limited space for renewable energy expect to import large amounts of hydrogen in the future.
But transporting hydrogen via ship is challenging. It has a very low energy density per volume. Hydrogen can be liquefied; however, that is energy intensive and inefficient.
Hydrogen could also be converted into other chemicals that act as a carrier. Ammonia is considered the most likely option. One molecule of ammonia consists of one nitrogen and three hydrogen atoms. Therefore ammonia - NH₃ - contains more hydrogen per molecule than pure hydrogen (H₂).
Plans for Ammonia Crackers in Germany and the Netherlands
Converting hydrogen and nitrogen into ammonia is done in the Haber-Bosch process, which is an established industrial process, usually based on hydrogen made from fossil fuels. Ammonia cracking is the reverse process - splitting ammonia back into nitrogen and hydrogen. In recent months BP has announced plans to build an ammonia cracker in Wilhelmshaven, Germany. The Port of Rotterdam in the Netherlands has announced similar plans supported by a large consortium of companies.
The idea is to produce hydrogen in places with a significant potential for renewable energy and use it to make green ammonia. The ammonia is then shipped to countries where hydrogen is needed and cracked back into hydrogen.
But taking a step back, we have to ask why green hydrogen is needed in the first place. One obvious use case for green hydrogen is to replace current fossil-based hydrogen. Yet the sector that uses the most hydrogen today is ammonia production.
It should be evident that it does not make sense to convert hydrogen into ammonia, convert it back to hydrogen, and then convert it to ammonia again. Instead, one would skip two conversion steps and use the imported ammonia directly.
Both planned ammonia crackers mentioned above are located close to existing ammonia production factories. Wilhelmshaven is only around 80 kilometers from Brunsbüttel, where Yara operates one of Germany's largest ammonia factories. Likewise, Yara also operates an ammonia factory in the Netherlands, not too far from Rotterdam. A second ammonia factory in the Netherlands is operated by OCI, which even happens to be one of the partners of the Port of Rotterdam for the planned Ammonia Cracker.
There may be a situation where hydrogen is more urgently needed than in ammonia production. An example would be steelmaking, where hydrogen could replace coal and thus have a higher potential to avoid carbon emissions.
But even then, it does not make sense to crack ammonia. Using imported ammonia to replace fossil ammonia and fossil-based hydrogen for steelmaking would still be more efficient. (Even more efficient would be to use the fossil gas directly in steelmaking.)
What happens when the existing ammonia production facilities implement cleaner production processes? Yara has announced plans to switch to blue hydrogen at its plant in Sluiskil in the Netherlands. This means implementing carbon capture and storage on the existing fossil-based hydrogen production. Leaving aside the considerable controversy around blue hydrogen - it'd still be preferable to replace the ammonia produced there with green imports and then use that blue hydrogen elsewhere, as you still skip two conversion steps.
I asked BP, OCI, and the Port of Rotterdam for a comment. The first two did not reply to my requests. Sjaak Poppe, energy transition spokesperson of the Port of Rotterdam, answered: "We expect that in the long run, much more ammonia will be imported than is going to be used locally (for fertilizer production, etc.), as ammonia is an attractive 'carrier' to ship hydrogen. So that's why we're studying an ammonia-cracking facility. You're right that it doesn't make much sense economically to have a cracker operating here while, at the same time, ammonia is being produced nearby."
This would imply that an ammonia cracker would only make sense to operate once all domestic ammonia production has been replaced with clean, imported ammonia. That means ammonia crackers will not be built anytime soon.
Haber-Bosch facilities in Europe become stranded assets
However, this scenario has more implications that are worth spelling out. Most notably, this would mean the end of ammonia production in hydrogen-importing countries. Most existing Haber-Bosch facilities in Europe would effectively be stranded assets, part of the fossil fuel infrastructure that is no longer needed in a decarbonized world.
Yet even assuming imports replace all ammonia production and there is excess ammonia production, one may still wonder whether cracking it back into hydrogen is the best path forward.
Another option would be to use more ammonia directly as an energy source, either by burning it or in a fuel cell. One industry considering renewable ammonia as an energy source is shipping. That comes with its own challenges - ammonia is toxic, and burning it in an engine causes NOx and N2O emissions that need to be controlled - but it would be more efficient than converting ammonia to hydrogen and using it as a fuel.
Another fact to consider when discussing ammonia as a hydrogen and energy carrier is: The Haber-Bosch process is exothermic, meaning that it releases energy in the form of heat. Conversely, ammonia cracking is an endothermic process that needs energy high-temperature heat - around 850°C.
This is not a good property of an energy carrier. Essentially, converting hydrogen to ammonia produces excess energy at the place where you have plenty of energy, while converting ammonia to hydrogen needs extra energy where it is scarce.
An industry insider I contacted indicated that ammonia crackers, if built, would best be co-located to existing industries to utilize waste heat from other processes. But that would likely not be at an import terminal at a port where no big sources of waste heat are available.
The conversion losses and the properties of the chemical reactions lead to a conclusion that does not play well with some of the hydrogen import scenarios currently discussed: While ammonia may be the best carrier to transport hydrogen by ship, it is just the best of many bad options. One may conclude that shipping hydrogen is generally not a good idea. An article at BloombergNEF by Michael Liebreich discusses this in more detail.
Before one considers ammonia cracking, one should ask some questions. Any imported clean ammonia should first be used to replace existing ammonia production. Direct use of ammonia as an energy source is preferable to converting it back into hydrogen. And if hydrogen is needed, one should consider importing it by pipeline or producing it locally.
Ammonia crackers may still find their role in the future. But they will likely remain a niche technology.
Update (2025-03-04): I made a video presentation about this topic: Ammonia Crackers make no sense and Shipping Hydrogen won't happen (YouTube)
Author: Hanno Böck
I don't like paywalls, and I guess you don't like them either. You can read my articles for free, but researching and writing them takes time and effort.
If you enjoy reading this newsletter regularly, please consider supporting my work. You can donate to support my work via Patreon. If you work for a company or organization that may want to sponsor the newsletter or advertise in it, please get in touch.
If you do not want to support me financially, that is, of course, also fine. You can still help me tremendously by sharing this newsletter. If you found this text insightful, please forward it to others or share it on social media, in your organization's chat, or wherever you find appropriate.
Brief
-
The Volts podcast published an interesting interview about electrolyzers.
-
The Distilled Newsletter received internal documents from propane industry groups, uncovering some of their PR strategies. Propane, also known as LPG or Autogas, is a fossil fuel, but apparently, this is not widely known in the population.
-
An MIT research team has developed a method to extract carbon dioxide from seawater to create negative emissions.
-
Gascade announced plans for a hydrogen pipeline connecting the island of Bornholm, Denmark, with Lubmin in Germany.
-
Danish company Greengo Energy announced plans for an energy park called Megaton in western Denmark. The project involves producing hydrogen with wind and solar energy and power-to-x technologies like the production of e-methanol.
-
The German company Ineratec has signed an agreement with MPC Container Ships from Norway to supply synthetic marine diesel oil (MDO) made from carbon dioxide and green hydrogen. A background article can be found at Fathom World.
-
Could drilling for naturally occurring hydrogen provide a clean source of the gas? An article in Science looks into it.
-
An article at Clean Energy Wire looks at the challenges for the decarbonization plans of the industry in India.
-
Technology Review looks at startups that plan to inject iron particles into the atmosphere, a proposed way to accelerate the breakdown of methane. Some scientists quoted are skeptical and think the evidence is not there yet.
-
Hydrogen Review reports that the steel company ArcelorMittal gets a lot of subsidies for green steel projects while at the same time building new blast furnaces in India that conflict with the company's own climate goals.