How to make Plastics without Fossil Fuels
Decarbonizing plastics and other petrochemical processes requires more than clean energy; it requires different input materials. A technology used in China's coal-based chemical industry could be an interesting building block for the future of plastics.
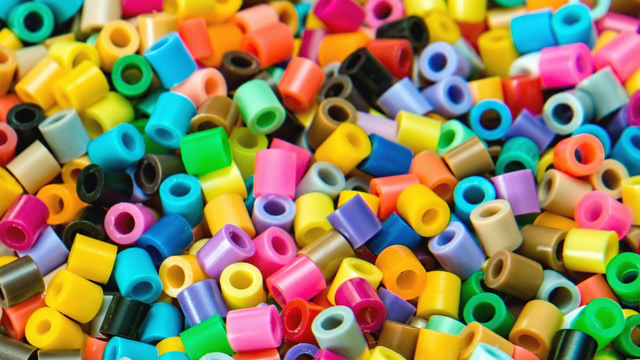
Decarbonizing the production of petrochemical products like plastics comes with unique challenges. The processes to make these products are energy intensive, and this energy usually comes from fossil fuels, but that is only part of the problem. The materials are made from fossil fuels. Eventually, these feedstocks must be replaced with alternatives.
Plastics come in different types with various ingredients and production methods. The two most common building blocks are the gases ethylene and propylene. Both are part of a group of chemicals called olefins.
Ethylene and propylene are usually created in steam crackers, large facilities that use heat to break up input materials. Typical inputs include naphtha, a product of oil refineries, or natural gas liquids, a by-product of gas drilling. Steam cracking happens at around 800 degrees Celsius (around 1500 degrees Fahrenheit). Heat is usually provided by burning fossil gas.
Steam cracking and other steps in the plastics production process could use electric energy from renewables, but it is essential to understand that this alone would not wholly decarbonize plastics. The products themselves contain carbon, leading to emissions after plastics have been used.
What happens to plastics after their end-of-life differs widely depending on the location. According to numbers from the OECD, around half of all plastic waste ends up in landfills. Around a fifth is burned in waste incinerators, while another fifth is mismanaged, meaning either uncontrolled burns or plastics that end up in nature. Only around 9 percent are recycled.
What do these different fates of plastics mean for their emissions? It should be obvious that plastic waste in nature is never a good thing, but it is less well-known that this can also be a significant source of greenhouse gas emissions.
A study published in the journal PLOS ONE in 2018 concludes that due to sunlight, plastics can break down into methane and ethylene, both potent greenhouse gases.
Landfills are also a significant source of methane emissions, though the role of plastics in landfill emissions is complicated. Most methane emissions from landfills come from the biogenic content of the waste. However, a mixture of plastics and organic waste can cause biogenic material that would otherwise turn into less harmful carbon dioxide to decompose into methane.
Waste incinerators or waste-to-energy plants are responsible for most of plastics' end-of-life emissions, even though only about a fifth of plastic waste is treated in them. Surprisingly, despite their high carbon dioxide emissions, waste-to-energy plants are sometimes seen as a form of green energy.
These emissions from end-of-life treatment are indirect emissions from the chemical and plastics industries. Another way to look at it is that plastics are themselves fossil fuels. It is important to realize that to decarbonize plastics and other petrochemicals fully, the carbon inside these products must come from other sources.
Technologies known as Power-to-X or Carbon Capture and Utilization (CCU) allow the production of hydrocarbons without fossil inputs. These technologies usually start with hydrogen, which can be produced with electricity by electrolysis of water. Hydrogen is then combined with carbon dioxide to form various other chemicals.
If these processes use clean electricity, they can provide drop-in alternatives to fossil fuels. Yet, CCU technologies require vast amounts of energy and are relatively inefficient. While better technologies may improve efficiency, converting one chemical into another will always come with losses.
Today's world electricity production just for chemicals
A study published in the scientific journal PNAS (Kätelhön et al., 2019) estimated that converting the worldwide petrochemical industry — not just plastics but also products like fertilizers — to CCU processes based on methanol would require between 17 and 32 petawatt hours of clean electricity per year. The world's total electricity production is currently at around 28 petawatt hours. In other words, the chemical industry would require about as much electricity as the world consumes today.
Scenarios published by the German Chemical Industry Association (VCI) come to similar conclusions. A roadmap published in 2019 assumes that the German chemical industry would need 685 terawatt hours of electricity for climate-neutral production by 2050. Today's electricity consumption in Germany is around 500 terawatt hours. In an updated publication in 2023, VCI came to somewhat lower but still high numbers (464 TWh, 508 TWh, and 325 TWh, depending on assumptions about electrification rate, used technologies, and the availability of biomass and recycling technologies).
It is hard to imagine that so much green electricity will be available for a single industry. At the very least, this raises the question of which CCU technologies are most efficient and what alternatives there are.
One path towards cleaner chemicals and plastics would be using steam crackers, electrifying the energy supply, and producing similar input materials synthetically.
There are currently no electrified steam crackers, but some companies have announced projects in that direction. The most advanced one is a project under construction at BASF's steam cracker facility in Ludwigshafen.
The electric cracker furnace has a power consumption of six megawatts. According to BASF, it will be able to process around 4 tons of hydrocarbons per hour. BASF's complete cracking capacity in Ludwigshafen is about 2 million tons annually. Therefore, the new electric furnace will power less than two percent of BASF's steam cracking capacity at that location. Scaling the electric furnace technology to BASF's capacity in Ludwigshafen would require between 300 and 400 megawatts — a lot of electricity, but not an implausible amount.
The bigger challenge will be replacing the inputs for the cracker. A possibility is to use Fischer-Tropsch synthesis to produce oil-like products. Fischer-Tropsch technology can synthesize a product similar to raw oil from hydrogen and carbon dioxide. These Fischer-Tropsch products could then be processed in refineries to produce the various products made from oil. Synthetic naphtha could then be processed in steam crackers to produce olefins. Of course, the refinery operations also need to be decarbonized.
The coal-based plastics industry in China
An entirely different path for olefin production exists that is primarily used in China. The country has limited oil resources, yet it has an abundance of coal.
Coal gasification is used to turn coal into a gas mixture called syngas, which is then converted into methanol. Methanol is the simplest liquid hydrocarbon, and a process called Methanol-to-Olefins allows making, well, olefins from methanol. In China, several such Methanol-to-Olefins plants based on coal gasification are operational.
Coal gasification is a very emission-intensive process to produce methanol. However, green methanol technology that makes methanol from carbon dioxide and hydrogen already exists at small scales.
The company Carbon Recycling International built the first such green methanol plant in Iceland in 2011. Lately, interest in green methanol has increased, primarily due to interest from the shipping industry, which wants to use it as a cleaner fuel. Combined, green methanol technology and Methanol-to-Olefins plants could provide a way to produce olefins and, subsequently, plastics.
One of the most interesting chemical industry decarbonization projects is currently being built at the world's largest Methanol-to-Olefins plant, located in Lianyungang, China. The plant's operator, Jiangsu Sailboat, is collaborating with Carbon Recycling International from Iceland to build a CO₂-to-Methanol plant with a capacity of 100,000 tons of methanol per year. It will replace some of the methanol currently produced via coal gasification.
This project does not provide a fully clean production chain. It does not use green hydrogen. Instead, it uses hydrogen and carbon dioxide from existing chemical processes at the facility. Also, for climate-neutral production, electricity and the energy needed in the Methanol-to-Olefins process would have to come from clean sources. Still, the technology will reduce emissions compared to the existing coal gasification.
Green Methanol-to-Olefins is more efficient than Fischer-Tropsch and steam cracking
The green version of the Methanol-to-Olefins route would be more efficient than doing the same with steam cracking. The previously mentioned reports and scenarios by the German Chemical Industry Association (VCI), unfortunately only available in German, give some interesting insights.
In its 2019 roadmap, VCI assumed that the primary technology used in a climate-neutral future would be Fischer-Tropsch synthesis with steam cracking. I once interviewed a representative from VCI for another publication, and he explained that the motivation for this was that "we already have the crackers." In other words, the German chemical industry saw an advantage in using its existing assets. (He also mentioned chemical recycling via pyrolysis as a reason to use steam cracking, which we will discuss later.)
In a report by a later project called Chemisty4Climate, also led by VCI and published earlier this year, they looked into these two technologies in more detail. The report clearly states that using Methanol-to-Olefins technology would be more energy efficient and require less green hydrogen.
But while the Methanol-to-Olefins route would have somewhat lower energy needs, it would still require enormous amounts of electricity.
Reducing the amount of plastic produced and used can help. However, one should be wary of unintended consequences. Replacing plastics with even less climate-friendly materials should be avoided. It is, for example, not a good idea to replace single-use plastics with single-use glass, which has even higher carbon emissions and is also challenging to decarbonize.
Potential alternatives for plastic feedstocks are biomass and increased recycling, but both have natural limitations.
Various forms of biomass and bioenergy could provide drop-in replacements for all fossil fuels. However, whether biomass is climate-friendly depends on many factors, like land use impacts and fertilizer use. Using waste biomass is generally a good idea, but its availability is limited.
Making plastics from biomass can happen in various ways, and discussing them is beyond the scope of this text. It is possible to make the same raw materials, like olefins, that existing plastics production uses or to produce entirely new types of plastics with a different chemical composition, allowing for more efficient production pathways.
Plastic recycling rates are relatively low, though differences between countries are substantial. They are particularly low in the United States, where only four percent of plastics are recycled. Raising the recycling rates of the currently lowest-performing countries would be a substantial improvement that could save energy and fossil feedstocks.
A problem with most of today's mechanical plastic recycling methods is that they work best with pure plastic streams composed of a single type of plastic with few impurities. However, plastic waste is often a mixture of different plastic types, with limited recycling potential.
Chemical recycling - still better than burning?
Technologies known as chemical recycling, sometimes also called advanced recycling, promise to provide a way to process mixed plastics or even mixed waste. These technologies would break down plastics and potentially other types of waste into more basic chemicals that could be feedstock material for new plastics.
The leading technologies proposed for chemical recycling are pyrolysis and gasification. They have a somewhat troubled history, with many high-profile failures, and many environmental organizations are rather critical of chemical recycling. Furthermore, many existing uses of these technologies are not about making new products. They use the results of these processes as energy sources. Sometimes technologies are called "chemical recycling" but are, in fact, just other forms of waste incineration.
Still, considering the highly energy-intensive CCU technologies and the limited availability of other renewable resources, using as many carbon molecules from waste to make new products as possible is a desirable goal. And even most critics would probably agree that chemical recycling, if the technology works, is better than burning waste and producing new plastics from fossil fuels.
Interestingly, the two primary chemical recycling technologies also have implications for the two different olefin production routes discussed earlier. Pyrolysis produces a mixture of a gas fraction, an oil fraction, and solid carbon residuals. Pyrolysis oil, the main product, could be used in steam crackers, while the smaller gas fraction, so-called syngas, could be turned into methanol. Gasification technology only produces syngas, which could be turned into methanol.
Therefore, chemical recycling using pyrolysis would work well with a mixture of steam cracking and Methanol-to-Olefins technology, while gasification would only need the latter.
Even with optimistic recycling scenarios and new recycling technologies, some waste that cannot be recycled will likely be left. However, it is still desirable to prevent the carbon content of that waste from ending up in the atmosphere.
Carbon capture for waste incinerators
Waste incineration could be coupled with carbon capture technology, and then carbon dioxide could be permanently stored (Carbon Capture and Storage, CCS) or used as an input for the CCU technologies. The latter would be a form of CO₂ recycling.
All CCU technologies require CO₂ to begin with, and this is a substantial challenge. Today, carbon dioxide could come from industrial sources. But eventually, other industries will need to decarbonize as well, so those sources will not be available and are not an option in a climate-neutral future.
Therefore, CCU technologies can only rely on a few carbon dioxide sources: biomass, waste, or direct air capture. The first two have limited availability. Direct air capture, meaning taking CO₂ directly from the air, is costly and energy-intensive. Carbon capture in waste incinerators is an interesting option here.
Any form of carbon capture for waste incinerators comes with substantial challenges. Combustion processes produce a mixture of gases, and the main content of an incinerator's flue gas is not carbon dioxide; it's nitrogen. Separating carbon dioxide from nitrogen and other gases is energy-intensive. I discussed the nitrogen issue in an earlier newsletter about CCS.
Currently, there are no waste incinerators with carbon capture technology operational. The city of Oslo had long planned to equip the Klemetsrud waste-to-energy plant with CCS, but the project has recently been put on hold due to cost increases.
In the German town of Zella-Mehlis, a local public waste management company plans to equip a waste incinerator facility with a small carbon capture facility and use the resulting carbon dioxide to synthesize methanol. Construction started this year, and plans are to have it operational in 2024. However, only a tiny fraction of the incinerator's carbon dioxide will be captured and used.
Decarbonizing plastic production will not just require electrifying production processes and provide that electricity with renewable energy. It will ultimately also require replacing fossil fuel feedstocks with alternatives. Carbon capture and utilization technologies based on green hydrogen and CO₂ can provide these feedstocks, but the electricity requirements are staggering. Biomass, improved recycling rates, and new recycling methods can help, but the challenges are still enormous.
Author: Hanno Böck
I don't like paywalls, and I guess you don't like them either. You can read my articles for free, but researching and writing them takes time and effort.
If you enjoy reading this newsletter regularly, please consider supporting my work. You can donate to support my work via Patreon. If you work for a company or organization that may want to sponsor the newsletter or advertise in it, please get in touch.
If you do not want to support me financially, that is, of course, also fine. You can still help me tremendously by sharing this newsletter. If you found this text insightful, please forward it to others or share it on social media, in your organization's chat, or wherever you find appropriate.
Thanks for reading my newsletter. I am experimenting with online lectures from some of the newsletter's content. If you want to check them out, subscribe to the YouTube channel "Decarbonize Everything". A video about plastics will be available soon.