Why the owners of a Shipping Company are investing in Fossil-Free Plastics
A. P. Møller Holding, the largest shareholder of Maersk, has launched a green plastics startup called Vioneo. It wants to build a Methanol-to-Olefins plant in Belgium - the first such factory in Europe.
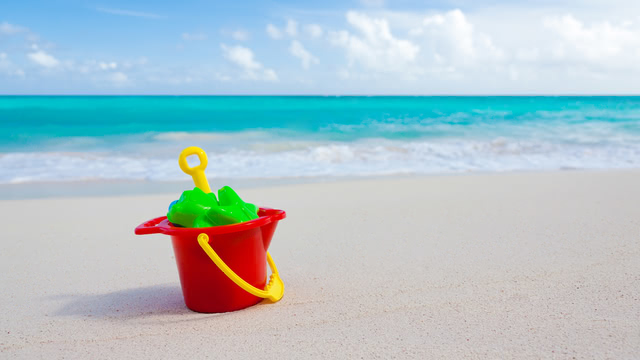
The use of fossil fuels for the production of plastics and other petrochemicals is, in some sense, quite different from other uses of fossil fuels. Usually, we associate fossil fuel use with energy. While the petrochemical industry consumes plenty of fossil fuel energy, it uses even more oil and gas to make the molecules that end up as its products. Plastics are not just made with fossil fuel energy; they are fossil fuels.
While the carbon content in products like plastics is not released as CO₂ during production, in many cases, it still eventually ends up in the atmosphere. Most plastic products are either burned in waste incinerators or landfilled at their end of life.
Waste incinerators are a significant and often underestimated source of CO₂ emissions. In poorly managed landfills, plastics can cause the formation of potent greenhouse gases like methane and ethylene, causing even more harm. It would, therefore, be desirable to avoid both the use of fossil fuel energy and fossil feedstocks in the chemical industry.
Plastics are not just a concern due to their climate impact. In recent years, new research has highlighted the health risks of plastic pollution in our environment. A study published last year in the New England Journal of Medicine (NEJM) found convincing evidence that microplastics in arteries increase the risk of heart attacks and strokes (Marfella et al., 2024).
Limiting the production of plastics would help to reduce climate and health impacts. Yet, while there certainly is a lot of avoidable plastic consumption, it is difficult to imagine a modern world without plastics.
Traditionally, Plastics are made with Steam Crackers
The most important building blocks for plastics are the two gases ethylene and propylene, which are part of a group of chemicals called olefins. Ethylene and propylene are usually produced in steam crackers.
Steam crackers tend to use different inputs in different parts of the world. In the United States, steam crackers often use ethane, a byproduct of fossil gas production. In Europe, it is more common to use naphtha made from oil.
To avoid emissions from plastic production, a first step would be process electrification. In 2024, BASF started the world's first electric steam cracker furnace. However, it is a relatively small pilot facility, and BASF has not announced any plans for a scale-up.
Yet, even electric steam crackers would not replace the fossil feedstocks. In theory, steam crackers could run on naphtha made from green Hydrogen and carbon dioxide via a Fischer-Tropsch process. However, while this may appeal to companies with existing steam crackers, it does not appear to be the most efficient option, as I have discussed previously.
A better way may be to utilize green Methanol, which can either be biomethanol, e-methanol made from Hydrogen and carbon dioxide, or — with some caveats — Methanol made via waste gasification. Methanol-to-Olefins plants that convert Methanol into ethylene and propylene are an established technology, but they are currently only used in China in combination with coal gasification.
The first movers towards utilizing this technology for greener plastic production are not traditional chemical companies. Vioneo, a startup founded by the Danish investment firm A. P. Møller Holding, wants to build a Methanol-based fossil-free plastic production plant in Antwerp in Belgium. Another startup called Blue Circle Olefins plans to build a methanol-to-olefins plant in the Netherlands. Unlike Vioneo, Blue Circle Olefins does not plan to build a full plastic production chain. Instead, it plans to collaborate with existing polymer producers.
A. P. Møller Holding, the company behind Vioneo, is primarily known for being the largest shareholder of Maersk, the world's second-largest container shipping company. But A. P. Møller Holding is also an investor in multiple other companies. It calls itself a "purpose-driven investment company" and names the energy transition as one of its goals on its web page. Whether all of its investments are aligned with this goal can certainly be questioned — A. P. Møller Holding owns 21% of the offshore oil drilling company Noble. However, the company has also invested in multiple cleantech startups.
That a company with connections to shipping giant Maersk would invest in Methanol-based technologies is no coincidence. Green Methanol is widely seen as a promising future clean shipping fuel. And Maersk is one of the names often associated with it.
Since 2021, Maersk has ordered multiple ships with dual-fuel motors capable of utilizing Methanol. Yet, more recently, Maersk has also ordered new LNG-powered ships, raising questions about its commitment to green fuels.
Still, Maersk is an important player in the green Methanol market. The shipping company has invested in startups like Waste Fuel, a US company developing technologies to turn agricultural and municipal waste into Methanol, and C1, a German company working on more efficient Methanol synthesis processes. Furthermore, Maersk has announced Methanol offtake agreements with the Chinese renewable energy companies LONGi and Goldwind.
I interviewed Alex Hogan, CEO of Vioneo, for this article. According to Hogan, Maersk's involvement in the green Methanol market led to a situation where the company assumed it could source more green Methanol than it would need. "And then our owner, A. P. Møller Holding, asked: 'What else can we do with it apart from using it as a fuel?'"
MtO was first developed to utilize Coal
Making plastics from Methanol is not a new idea, but the history of this technology has little to do with climate mitigation and cleantech. It was developed in the 1980s in Germany as a way to utilize coal.
Methanol can be produced via coal gasification. Making Methanol from fossil gas is already an emission-intensive process, but making it via coal gasification is three times as bad. A technology called Methanol-to-Olefins or MtO allows the conversion of Methanol into ethylene and propylene, the most important source material for plastic production.
While MtO was first developed and tested in Germany, the technology was scaled up in China. Today, more than a dozen Methanol-to-Olefins plants are operational in China. A company that played a significant role in this development is Honeywell, a US technology provider. Honeywell's subsidiary UOP has provided the technology for multiple MtO plants in China, including the largest one, Jiangsu Sailboat. The Jiangsu Sailboat MtO plant is also the location of a CO₂-to-Methanol plant built by Carbon Recycling International, an E-Methanol company from Iceland. While that doesn't make Jiangsu Sailboat clean, it lowers the emissions at least a little bit.
In January this year, Vioneo announced that it chose Honeywell's MtO technology for its plant in Belgium. Vioneo writes: "This facility will use green methanol from renewable energy-based Hydrogen and biomaterials and will be powered by renewable electricity."
Vioneo furthermore mentions an interesting detail: "Vioneo will also deploy Honeywell's light olefins recovery process (LORP) and olefins cracking process (OCP) to ensure high-purity ethylene and propylene output while capturing and reusing byproducts."
Chemical processes often generate unwanted byproducts. Today, these are often burned to generate heat. Given that Vioneo plans to power its process with electricity — and that its green methanol feedstock is a major cost factor — "capturing and reusing byproducts" seems logical to utilize as much of the material as possible and avoid burning byproducts.
Next Door to the new Steam Cracker
Vioneo plans to build its facility at the Vopak Energy park in the Port of Antwerp. It is located only about two kilometers north of a site where another company wants to make plastics.
The chemical company INEOS is building a new steam cracker named Project One in Antwerp. INEOS also pitches its steam cracker as a climate solution and writes: "If we want to tackle climate change, we need to focus on solutions that dramatically reduce carbon emissions right now."
INEOS argues that its steam cracker, which, unlike most other crackers in Europe, will utilize ethane instead of naphtha, has lower emissions than most of its competitors. While it is true that ethane crackers can have slightly lower emissions compared to naphtha crackers, it does not change the fact that Project One will depend on fossil fuels both for its energy and its feedstock.
A coalition of environmental NGOs led by the organization ClientEarth challenged Project One legally and had some success in delaying the project. (Discussing Project One in detail may be the topic of a future newsletter.)
That Vioneo plans to build its fossil-free plastics plant right next to the site of a fossil plastics plant is, as Vioneo's CEO Alex Hogan told me, pure coincidence. The location is merely attributed to the fact that Antwerp is one of the largest and most attractive sites for chemical plants in Europe. "They (A.P. Møller Holding) were looking for a site where chemical plants were already based," Hogan told me. "Antwerp is a deep-sea port and we would be getting our feedstocks initially via vessel."
Before joining Vioneo, Alex Hogan worked for INEOS Olefins and Polymers. Understandably, he did not want to comment on his previous employer's business. He told me, however, that he was not directly involved in Project One.
A Fossil-Free Plastics Plant of an Industrial Scale
Plastics based on biological feedstocks are not a new development, but what Vioneo is planning is unique in multiple ways. Most previous attempts to produce bio-plastics have created plastics with a chemical composition different from fossil-based products.
A Methanol-to-Olefins plant produces the same ethylene and propylene gas as a steam cracker. Therefore, Vioneo would, if successful, produce a direct drop-in replacement for the most common types of plastics. It's the same plastics, just made from a biogenic or potentially CO₂/Hydrogen-based input material.
It is also noteworthy that Vioneo does not plan to build a pilot-scale plant but directly wants to go to an industrial scale, using technology that is already available today.
According to its announcements, Vioneo plans a production capacity of around 300,000 tons of plastics per year for its plant in Antwerp. While it is not a huge facility, its production volume is comparable to that of some of the smaller steam crackers and existing MtO facilities.
Yet, if Vioneo wants to operate its plant, it needs to be able to sell its product at a premium. "Let's face it, it does not come for free," Alex Hogan told me.
For a company like Vioneo that wants to pioneer a new, climate-friendly technology that comes with additional costs, there are two main ways how they can operate. Climate policy could support their business model, for example, through carbon pricing (from which the EU chemical industry is currently largely exempt for their indirect emissions caused by the carbon embodied in their products, as they are not part of the Emission Trading System), quotas for green products, or other support schemes.
The other option is to find offtakers that are willing to pay a premium to support their brand and be able to advertise greener products. "We are in advanced discussions with many global brands about offtake," Hogan said.
Vioneo wants to offer them something unique that has been the source of some controversy between brands and environmentalists. Vioneo wants to offer, as they write in a press release, "a fully segregated and traceable product offering."
When chemical companies move towards greener feedstocks, it is challenging for them to convert full production facilities. Instead, they may use small amounts of green feedstocks within their existing, fossil-based plants. In order to be able to sell green products at a premium, many chemical companies are following a mass-balance approach. They are selling a certain share of their product as green, even though it is part of a mixed production chain.
Lately, the toy maker Lego has come under fire from some environmentalists for using such a mass balance approach.
Such mass balance approaches are controversial for a variety of reasons. Without proper oversight, double counting and a lack of additionality are a common problem of such systems. (Regular readers of this newsletter may be aware of similar concerns about green electricity certificates.)
"One of our unique selling points is: There is no mass balance here," Vioneo's CEO Alex Hogan told me. "Everyone in the business understands that mass balance comes with a lot of questions. It's not as easy to convince someone of the integrity of the process if it's mass balance."
Biomethanol from Asia
Vioneo has not named any specific suppliers for its Methanol. However, according to previous media reports, the company will likely start by sourcing Biomethanol from Asia.
Hogan told me that he would eventually like to see a European supply chain and also use E-Methanol — made from CO₂ and Hydrogen. Currently, he does not see that as an option.
(I covered some recent developments around E-Methanol production in Europe in my last newsletter.)
Using Methanol made from biomass may come with its own controversies. Any form of biogenic resource is only as green as its production methods. Land use changes, deforestation, and competition with food production can quickly evaporate any climate benefit. While not directly connected to Methanol, lately, there have been increasing concerns about certification fraud for biofuels from used cooking oil, which, in many cases, may actually be virgin palm oil with a high carbon footprint.
Hogan told me that they are currently in conversations with a large Asian producer that would use crop waste for its Biomethanol production. Asked about such concerns, Hogan told me: "I think it comes down to the amount of diligence you do. We are auditing them very thoroughly. We will make sure through our supplier conduct that regular inspections are made to make sure that what we are paying for is what we contractually agreed."
EU wants to "substitute virgin fossil materials in plastics"
Besides convincing brand owners to pay a premium for fossil-free plastics, Vioneo is also hoping for policy support. According to a press release, Jan Secher, Chair of Vioneo, said: "Success hinges on the commitment of customers, partners, support from policymakers through regulatory frameworks and access to low-cost green energy and financial backing."
When asked about how optimistic he is that policies supporting business models for fossil-free plastics will come within the EU, Alex Hogan was quite confident.
"I know it's gonna come," Vioneo's CEO said. "Over the next 2 years, you will see legislation come in. I don't know what form yet, but it's coming."
Hogan mentioned the EU's Packaging and Packaging Waste directive (PPWR) which points to future requirements for recycled and bio-based plastics. He also said that he expected support from the EU's upcoming Clean Industrial Deal.
I interviewed Hogan the day before the European Commission presented the Clean Industrial Deal. It contains these words: "To move away from fossil materials, it is vital to mandate the use of new raw material sources like recycled and bio-based materials to substitute, for example, virgin fossil materials in plastics." It certainly sounds like the European Commission is on board pushing policies that support fossil-free plastics production.
If things work out as planned, production in Vioneo's fossil-free plastics plant in Belgium could start in 2028. However, no investment decision has been made yet. "Our final investment decision will be made by the end of this year", Vioneo's CEO Alex Hogan told me.
Author: Hanno Böck
I don't like paywalls, and I guess you don't like them either. You can read my articles for free, but researching and writing them takes time and effort.
If you enjoy reading this newsletter regularly, please consider supporting my work. You can donate to support my work via Patreon. If you work for a company or organization that may want to sponsor the newsletter or advertise in it, please get in touch.
If you do not want to support me financially, that is, of course, also fine. You can still help me tremendously by sharing this newsletter. If you found this text insightful, please forward it to others or share it on social media, in your organization's chat, or wherever you find appropriate.
Canadian Waste-Gasification-to-Methanol Project in Trouble
One way of sourcing Methanol for alternative plastic production pathways, like the one discussed in the article above, would be to utilize waste gasification technology. In my last newsletter, I mentioned that the Spanish energy company Repsol wants to build a Waste-Gasification-to-Methanol plant with technology from the Canadian company Enerkem.
I also mentioned that one project with Enerkem's technology was under construction in Canada. At the time, I was unaware that the mentioned project is in a lot of trouble. According to the newspaper La Presse, construction at the project named Recyclage Carbone Varennes (RCV) is currently on hold as the company was unable to secure funding.
Things were already not looking too bright for Enerkem. Its only operating plant in Edmonton, Canada, was shut down last year. Plans for a project in the Netherlands that was originally announced as a Waste-to-Methanol plant and later as a Waste-to-Jet-Fuel facility were silently dropped. A company called Dimeta wanted to build two Waste-to-DME (Dimethyl Ether) plants with Enerkem's technology in the Netherlands. However, Dimeta no longer exists.
In light of these developments, it is even more noteworthy that Repsol appears to believe it can use Enerkem's technology successfully. Repsol has announced an investment decision for its plant in January. According to La Presse, Repsol now effectively controls Enerkem.
Video about Ammonia Crackers
I previously discussed the idea of using Ammonia as a Hydrogen carrier and Ammonia Crackers to convert Ammonia back into Hydrogen. It is a questionable idea, particularly in places where existing Ammonia production facilities already exist.
Air Liquide has recently announced that it received support from the EU Innovation Fund for building an Ammonia Cracker in Antwerp, Belgium. (To avoid confusion: an Ammonia Cracker is not the same as a Steam Cracker. The main article above discusses the construction of a Steam Cracker in Antwerp, but this is unrelated.)
I talk about this in a video presentation here:
Ammonia Crackers make no sense and Shipping Hydrogen won't happen (YouTube)