From Coal enabler to the Minimal Green Methanol Economy
While it does not get as much attention as hydrogen, green methanol could play a crucial role in a climate-neutral industry. Ideas for a Methanol Economy have been around for decades, but the implementation challenges should not be underestimated.
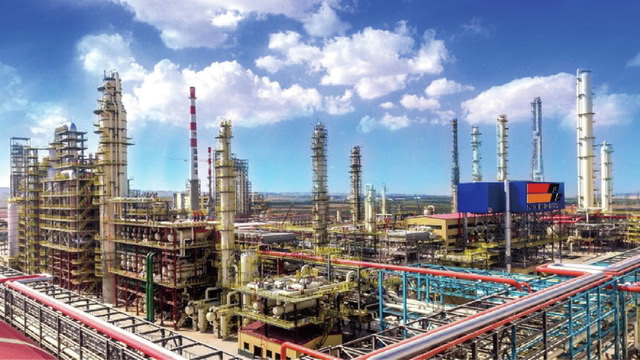
In 1986, the chemist Friedrich Asinger published a book proposing that the "mobilization of coal" by converting it into methanol could play a major role in the energy system and the chemical industry. Making methanol from coal causes very high carbon dioxide emissions. Yet, while the harmful effects of CO₂ on the earth's atmosphere were known at the time, they were not a topic widely discussed.
At the time, the US oil company Mobil was experimenting with technologies that would allow the production of fuels and plastics from coal through the synthesis of methanol. Those Methanol-to-Gasoline and Methanol-to-Olefins processes were first tested in a pilot plant at a refinery in Wesseling, West Germany, operated by the Union Rheinische Braunkohlen Kraftstoff AG.
Asinger already briefly mentions that cheap hydrogen would allow the production of Methanol from CO₂ and even the idea of separating CO₂ from the air. Another chemist expanded on these ideas much later.
The Methanol Economy as an alternative to the Hydrogen Economy
In 2005, Nobel Prize winner Georg Olah wrote an essay titled Beyond Oil and Gas: The Methanol Economy and later a book with the same title. Olah saw the Methanol Economy as an alternative to the back-then already popular idea of a Hydrogen Economy. He pointed out that hydrogen is difficult to store and transport. Physical realities do not change: those are still major challenges for clean hydrogen today.
Methanol, an alcohol with the chemical formula CH₃OH or MeOH, is a widely traded chemical commodity, usually used to make other chemicals like formaldehyde. It is also used as a fuel additive. It is commonly made from syngas, a mixture of carbon monoxide and hydrogen. That syngas is either made from fossil gas or coal.
As indicated in his paper's title ("Beyond Oil and Gas"), Olah's idea was to eventually produce methanol without fossil fuels. Olah saw "the recycling of CO₂ from industrial exhausts or natural sources, and eventually from the air itself" as a promising way to replace fossil resources.
Some of Olah's ideas appear obsolete today. He proposed, for example, to run laptops or cell phones on methanol fuel cells. Yet, while methanol receives nowhere as much publicity as hydrogen, many energy experts believe that green methanol could play an important role in a future decarbonized economy.
Olah lived long enough to watch the company Carbon Recycling International taking the first steps to make his vision a reality in Iceland, a country with abundant, clean, and cheap renewable energy sources. He was an early advisor to the company and participated in the groundbreaking ceremony in 2009 for the first renewable methanol plant, which was named after him. It uses renewable electricity to make hydrogen and, in a subsequent process, converts hydrogen and CO₂ to methanol. Methanol made that way is commonly called e-methanol.
The George Olah Renewable Methanol Plant went online in 2012 and remains one of the few existing Carbon Capture and Utilization (CCU) projects. However, with a capacity of 5,000 tons of methanol annually, it is tiny compared to industrial fossil methanol facilities.
Carbon Recycling International had plans to build a much larger e-methanol plant in Iceland with a capacity of around 80,000 tons. It was at the time (2011) discussed as an alternative to a controversial aluminium plant that was never finished. However, these plans never materialized, and it was only much later that the Icelandic energy startup could scale up its technology.
In recent years, green methanol has been proposed as a future clean fuel for the shipping industry. Pioneered by ferry operator Stena Line and later pushed by container shipping giant Maersk, methanol seemed like a promising option for the future of clean shipping.
Lately, however, the shipping industry's ambition to use green methanol as a fuel has seen some setbacks. Maersk went back to ordering LNG ships operated on fossil gas, and the Danish wind energy company Ørsted canceled plans for the green methanol factory FlagshipOne in Sweden.
Green Chemicals, Energy Storage, Methanol-to-X
Renewable energy usually comes in the form of electricity. When possible, electrification is often the best path towards emission reduction. It is simply the most efficient way, as it avoids the inherent inefficiencies of combustion processes.
However, there are use cases where electrification will likely not be feasible. Even with optimistic assumptions about future batteries, their energy density will unlikely be enough to power container ships or long-distance aviation. In all likelihood, some use cases will require chemical energy carriers.
The simplest chemical energy carrier is hydrogen. While hydrogen has a high energy density per weight, it has a very low energy density per volume. That makes hydrogen challenging to transport and store. Methanol is the simplest way to store energy as a liquid, which makes handling it much easier.
Methanol could be used in difficult or impossible-to-electrify sectors. In some applications - like shipping - it can directly be used as a fuel. The same is not true for aviation, as even the energy density of methanol is not high enough. Methanol-to-Kerosene/Methanol-to-Jet-Fuel technology is one of the options discussed for making e-kerosene/e-SAF. However, this technology is not yet available at an industrial scale.
Methanol could also serve as an energy storage technology to balance intermittent renewables. Furthermore, it could be a fossil-free feedstock for the chemical industry.
Methanol's existing use as a chemical feedstock
Methanol is already an essential commodity in the chemical industry. Today, almost all of it is produced either from fossil gas or coal.
Notably, methanol causes emissions both during production and after its use, as it contains carbon, which, in many cases, eventually ends up in the atmosphere. According to numbers from the Methanol Institute these end-of-life emissions are substantially higher than the production emissions for gas-based methanol production. For coal-based production, production emissions are higher. Overall, coal-based methanol production is almost three times as bad as gas-based production.
One might assume that the first use case for green methanol should be replacing fossil methanol used in the chemical industry. Interestingly, that is not necessarily the case.
One of Methanol's main uses in the chemical industry is the production of formaldehyde and its derivatives like formic acid, molecules with a relatively low internal energy. Going from low-energy CO₂ to methanol and then to formaldehyde could, therefore, be seen as a form of thermodynamic zig-zag that is needlessly lossy.
Avoiding that intermediate step would be attractive. Yet, attempts to make formaldehyde and formic acid directly from carbon dioxide have been researched, but so far, such technology has not been successfully deployed as an industrial process. (I learned this through LinkedIn comments from Paul Martin. Due to LinkedIn's poor search, I was unable to find those comments again.)
China's Coal-based Methanol Economy
A substantial part of the world's methanol production goes into a process to make olefins, which are precursors for the most common types of plastics. Methanol-to-Olefins technology is almost exclusively used in China, which brings us back to Friedrich Asinger's ideas for "the mobilization of coal".
China has limited oil and gas resources, but the country is rich in coal. China uses a variety of technologies that use coal to produce products that would otherwise be made from oil or gas. Most of these technologies start with the coal gasification process, which converts coal into syngas. Syngas is then often converted into other chemicals like methanol. (Some coal gasification facilities also produce methane, which can replace fossil gas.)
Due to this development, there exists a small but not entirely insignificant market for methanol-based cars in China, and a chemical industry based on methanol. Through processes like Methanol-to-Olefins and Methanol-to-Aromatics, Chinese chemical facilities make plastics and other products from coal.
The closely related Methanol-to-Gasoline technology has not seen major adoption in China, but it is used in some gas-rich countries to make liquid fuels from fossil gas. The largest Methanol-to-Gasoline facility is located in Turkmenistan. (In theory, this technology could make e-gasoline for cars - I have covered the Haru Oni project in Chile before - but the extreme inefficiencies compared to battery-electric vehicles make that unlikely.)
China's existing coal-based chemical industry is certainly not climate friendly, but these technologies are discussed as options for a fossil-free chemical industry. Using Methanol-to-Olefins technology and replacing inputs with green methanol could provide a path toward fossil-free plastics.
China's largest Coal-to-Olefins producer has already shown an interest in this technology path. This brings us back to Carbon Recycling International, the green methanol pioneers from Iceland.
After finishing a pilot plant in 2012, Carbon Recycling International built a few more small pilot plants as part of research projects. Yet, the first significant upscaling of their technology happened in China. In 2022, a 110,000 ton per year CO₂-to-Methanol plant started production at a steel plant in the Henan province of China. In 2023, another plant with a capacity of 100,000 tons annually went online at the Jiangsu Sailboat chemical facility in Lianyunggang, Jiangsu province, operated by Shenghong Petrochemical. And that facility is the world's largest Methanol-to-Olefins plant.
It should be mentioned that these plants hardly count as "green" methanol. Neither the energy to operate them nor the hydrogen is renewable. These facilities use hydrogen and carbon dioxide produced as by-products in other processes.
When I visited Iceland in 2022, Ómar Sigurbjörnsson from Carbon Recycling International explained to me that these developments still reduce emissions, as they replace methanol otherwise made via coal gasification. Considering the extremely high emissions of the coal gasification route, that is almost certainly true. Despite these caveats, it is noteworthy that China's largest Coal-to-Olefins operator is showing an interest in CO₂-to-Methanol technology.
Turning CO₂ into Methanol requires staggering amounts of energy
If you are convinced at this point that we should make Georg Olah's vision of a Methanol Economy based on CO₂ recycling and eventually capturing CO₂ from the air a reality, make fossil-free plastics, store methanol as an energy backup for the infamous "Dunkelflaute", and run ships, planes, and potentially even cars either directly or indirectly on methanol fuel, it is time to pour some cold water on it.
Green methanol faces multiple challenges. Turning CO₂ into methanol - or any other high-energy molecule - requires staggering amounts of energy, usually provided in the form of hydrogen. That is inevitably so, as carbon dioxide is a very low-energy molecule. Turning it into anything with a much higher energy content - like methanol - inevitably requires adding a lot of energy. No amount of research or innovation will change that, as it is dictated by the laws of thermodynamics.
While methanol compares favorably to other Carbon Capture and Utilization technologies, the amounts of energy required for anything resembling a Methanol Economy are enormous. A study by Arne Kätelhön et al, published in the scientific journal PNAS in 2019, estimates that converting the chemical industry towards CCU-based methanol would require between 17 and 32 Petawatt hours of clean electricity annually - roughly as much as today's world electricity production.
The second major challenge e-methanol faces is that it needs a source of CO₂. Historically, it has often been proposed to use existing emission sources. However, that is no long-term solution if methanol is used as a fuel or in products that will eventually degrade to CO₂ or be burned. It is, therefore, now commonly accepted that such carbon capture and utilization technologies can eventually only rely on CO₂ from biogenic sources - or direct air capture. The latter would substantially increase the already excessive energy needs of green methanol production.
Methanol further comes with the challenge of being easily mixed with water. Water is a by-product of the production process, and additional energy is needed to separate methanol from water via distillation. Furthermore, methanol storage needs to avoid contact with atmospheric humidity.
"All your Carbon shall be Methanol"
In a social media post, Tom Brown, an energy modeling researcher from the Technical University Berlin, shared some ideas for the future of green methanol. Brown's post starts with the words: "All your carbon shall be methanol". What Brown suggests is that a lot of carbon already stored in waste materials could be converted into methanol.
Various production pathways exist to make methanol from biogenic materials or other forms of waste. Historically, methanol was also called wood alcohol. Methanol from wood is a by-product of the Kraft process used in the pulp and paper industry.
Most pulp mills today simply burn that methanol by-product, which comes with various impurities, to generate heat. But that is not necessarily the best use of valuable methanol. A paper mill operated by Alberta-Pacific in Canada and another one operated by Södra in Sweden have implemented processes to upgrade this by-product to industrial-grade methanol.
In a report about renewable methanol published in 2021, the International Renewable Energy Agency (IRENA) estimates that applying this process to the whole global pulp and paper industry could produce over a million tons of methanol annually. (Around one percent of today's global methanol production.)
Another pathway for biomethanol production is the use of biomethane made from biogas. Converting biomethane to methanol can be done using the same process that is used to make it from fossil gas. Biogas can be made from agricultural or food waste via anaerobic digestion. Substantial volumes are also produced from corn, which is more controversial due to land-use impacts.
IRENA's report about renewable methanol also discusses hybrids of bio- and e-methanol production. Many bioenergy production pathways generate carbon dioxide as a by-product. Biogas, for example, comes as a mixture of around 40 percent CO₂ and 60 percent methane. When upgraded to biomethane, CO₂ is separated. Today, it is unfortunately often just vented into the atmosphere.
Instead of just converting biomethane into biomethanol, adding green hydrogen to the process could enable a combined bio- and e-methanol production process. While that would still require substantial amounts of clean energy, it avoids the need for more expensive CO₂ sources like direct air capture.
Another way to produce methanol is biomass or waste gasification. A technology quite similar to the previously mentioned coal gasification can be applied to convert a variety of carbon-based materials into syngas, subsequently also allowing the production of methanol. It is one of the technologies often discussed under the umbrella term "chemical recycling". (Confusingly, CO₂ utilization technologies are sometimes also called chemical recycling. Notably, George Olah used the term like that.)
Gasification technologies could potentially allow the conversion of cellulosic biomass that is difficult to utilize otherwise or mixed, unrecyclable waste into valuable chemicals like methanol. While not as energy-hungry as CO₂ utilization, gasification technologies still requires substantial amounts of energy, as they involve high temperatures. Similarly to the biogas route, it would be possible to increase yields by adding clean hydrogen, as the input streams usually do not have an ideal carbon-to-hydrogen ratio.
Waste and biomass gasification technologies have a troubled history. Failed projects like the Thermoselect plant in Karlsruhe (Germany) and the Air Products gasification project in Tees Valley (UK) gave waste gasification the reputation of a technology that never works. Waste gasification is, however, commonly used in Japan, but it is usually not used to make methanol. Instead, syngas is often burned to generate energy.
A waste-to-methanol plant in Spremberg (Germany) operated successfully between 1995 and 2007, but eventually could not compete with methanol made from cheap fossil gas. According to the limited information available on its old web page, the "Sekundärrohstoff-Verwertungszentrum Schwarze Pumpe" also used coal in the process, so the overall carbon footprint likely was not very favorable.
In 2010, a biomass gasification plant utilizing waste products from the pulp and paper industry went online in Piteå, Sweden. It produced dimethyl ether, a chemical closely related to methanol. It was shut down in 2016.
The company Enerkem has operated a waste-to-methanol plant in Edmonton (Canada) since 2016 and has announced plans for multiple similar projects. Yet, the plant in Canada was shut down earlier this year.
Waste and biomass gasification appears challenging. However, it would allow using many carbon-containing resources that, today, are often burned or landfilled.
Waste gasification as a potential energy source comes with an important caveat. Energy sources generated from mixed waste input are often considered second-generation biofuels. However, it is important to realize that substantial amounts of the carbon and energy content of mixed waste are of fossil fuel origin. Plastics and other petrochemical products are, essentially, just another fossil fuel.
It is interesting to consider how this can be accounted for. When waste is used to make new resources like methanol, one could say that this is a green product as long as the same amount of carbon that is extracted from materials like plastics ends up in new products at the end. Such processes will inevitably have losses, but utilizing mixed waste that contains partly biogenic carbon would make this possible.
Apart from using carbon-containing waste materials, improving the efficiency of the production process is another way to ease the extreme energy needs of green methanol production. The Berlin-based startup C1 is trying to do exactly that. By using a new type of catalyst developed with the help of quantum simulations, C1 hopes to increase the efficiency of the syngas-to-methanol conversion. C1 has recently announced the production of a first batch of methanol in a pilot plant at the chemical park in Leuna, Germany.
Even with efficiency improvements and utilizing as much carbon from waste resources as possible, green methanol will remain a limited resource and inefficient compared to electrification alternatives. Tom Brown, therefore, also talks about a "Minimal Methanol Economy" and summarizes his thread with the words: "Electrify everything. Use methanol with sustainable carbon for the rest. OK, also a bit of hydrogen for ammonia and steel."
E-Methanol development in China is gaining Momentum
Of course, visions of a green methanol economy do not matter if the technologies do not get deployed at scale. With Enerkem's shutdown of the world's only industrial waste-to-methanol facility and Ørsted's cancellation of the FlagshipOne e-methanol project, the news lately has not been great. One may see these developments as signs that green methanol is facing reality - or simply as signs of the fact that policy incentives are not yet sufficient to enable the technologies the world needs for the transformation to a climate-neutral economy.
Despite setbacks, other green methanol projects proceed. Significant development appears to be happening in China. Carbon Recycling International has recently announced another collaboration with two Chinese companies - Jiangsu Dafu and Guangdong Hydro Power - involving the construction of a 100,000 tons e-methanol facility and "the world's first hydrogen-methanol integrated equipment manufacturing project using renewable energy."
Chinese wind turbine maker Goldwind recently broke ground for a 500,000 tons e-methanol production plant in Inner Mongolia and has plans for another one with an annual capacity of a million tons. Chinese car maker Geely has received approvals for a 500,000 tons e-methanol plant. It remains to be seen how many of these projects are actually built, but it is a development worth watching, particularly given the fact that there is already plenty of experience with the downstream use of methanol in China due to the country's coal-based methanol sector.
Today, Chinese companies dominate solar cell production and are strong players in other cleantech areas like wind energy and electric vehicles. Chinas dominance in the solar market was, in all likelihood, a strategic decision early on, at times when many still believed that solar energy was something not to be taken seriously.
While many energy experts are convinced that green methanol technologies will be an important building block of a future clean energy system, Chinese companies appear to be busy making sure that they play an important part in it.
Update: I gave a talk about Green Methanol at the 38th Chaos Communication Congress (38C3) in December 2024, which was largely based on the content of this article. A video recording is available here and on YouTube.
Author: Hanno Böck
I don't like paywalls, and I guess you don't like them either. You can read my articles for free, but researching and writing them takes time and effort.
If you enjoy reading this newsletter regularly, please consider supporting my work. You can donate to support my work via Patreon. If you work for a company or organization that may want to sponsor the newsletter or advertise in it, please get in touch.
If you do not want to support me financially, that is, of course, also fine. You can still help me tremendously by sharing this newsletter. If you found this text insightful, please forward it to others or share it on social media, in your organization's chat, or wherever you find appropriate.
Brief
-
Previously, I had covered a misleading infographic with a log scale. I have now also made a short video about it. (Live recording, please excuse the audio quality.)
-
Glassmaker Verallia has recently inaugurated a fully electric glass furnace in France. Glass furnaces usually burn fossil gas to melt their product, fully electric glass furnaces are only used for special glasses in small facilities. Attempts to electrify larger ones have turned out to be difficult. An industry representative previously told me that a failed project in the US more than a decade ago was a "real trauma for our industry". With 180t/day, Verallia's furnace is larger than most existing electrified glass furnaces but still small compared to larger ones. Other companies bet on hybrid furnaces. For comparison, Ardagh's NextGen furnace (mostly electric, some gas) in Germany has a capacity of 350t/day.
-
Equinor scraps plans for blue hydrogen production in Norway, citing a lack of demand.
-
Shell scraps plans for blue hydrogen production in Norway, citing a lack of demand.
-
Voters in Zürich, Switzerland, approved plans for a CCS facility at a sewage sludge combustion plant in a referendum. Half of the CO₂ could be stored in concrete waste, a process developed by Neustark, which I had covered before. The other half could go to a storage facility in Denmark.
-
The cement company Holcim invests in Sublime Systems. Cement production involves the release of CO2 from chemical processes, which is why it is often named as a sector that requires carbon capture and storage. The technology from Sublime Systems would allow cement production without carbon emission by utilizing calcium silicate inputs.
-
A steel company in the US wants to replace coal with plastic waste in a blast furnace in Pennsylvania, as Canary Media reports. It certainly does not sound like a good idea. Any emission reductions will likely be modest. Yet, it appears the company may receive subsidies via the US Inflation Reduction Act.
-
CBC Canada reports that construction for a hydrogen-based green steel plant in Ontario, Canada, by ArcelorMittal has not started yet, despite previous announcements from the company to phase out coal at the site by 2028.
-
Last but not least, some good news from the steel sector: a UK court has blocked plans for a new metallurgical coal mine.