Carbon Removal with Demolished Concrete
At a recycling facility on the outskirts of Berlin, carbon emissions from biomethane production are stored in construction waste. The Swiss company Neustark hopes that its technology will play a part in a future carbon removal industry.
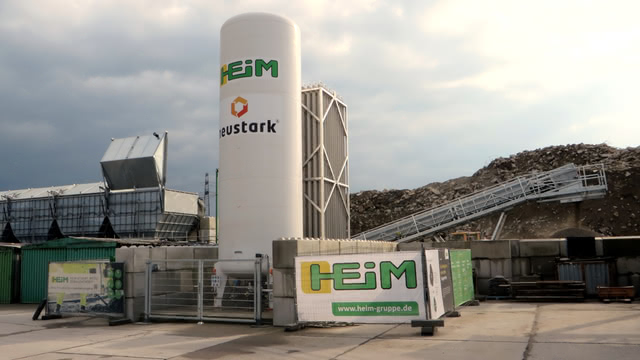
It is not an area of the German capital Berlin that many of its visitors will ever see: in an industrial area in Berlin's outer district Marzahn, the recycling company HEIM operates a construction waste landfill.
HEIM collects debris from teardowns and sells it as new building material. Thomas Drechsler, the site's operations manager, says the company's goal is to re-use the material as much as possible, preferably in high-value applications. However, he complains that German regulation often makes a higher-value use difficult.
Since late 2023, the recycling facility has been using its waste in a novel and unexpected way: it serves as a storage material for carbon emissions. Heim collaborates with the Swiss company Neustark, which has developed a technology that lets carbon dioxide react with demolished concrete. It permanently neutralizes the greenhouse gas and prevents its release into the atmosphere.
CO₂ from Biomethane plants is stored in demolished Concrete
While Neustark collaborates with recycling companies like HEIM to store CO₂, they also need a source of the greenhouse gas. Currently, Neustark's preferred sources of CO₂ are biomethane facilities.
Biomethane is made from biogas, which is produced by the fermentation of inputs like agricultural waste or — more controversial and less climate-friendly — crops like corn. It is a mixture of primarily methane and carbon dioxide. To produce pure biomethane from biogas, both gases need to be separated. Therefore, biomethane facilities have almost pure carbon dioxide as a by-product. Today, biomethane facilities often simply release it into the atmosphere.
Neustark's plant in Berlin-Marzahn uses CO₂ from a biomethane facility near Dresden. By using biogenic emission sources, Neustark can claim that its technology removes carbon dioxide from the atmosphere and generates negative emissions.
Neustark already operates several facilities in Switzerland. The plant in Berlin-Marzahn is the first abroad. They want to build more, but Neustark's representatives have a complaint that many cleantech companies in Germany will share: slow approval processes.
"Compared to Switzerland, the approval took three to four times as long here", said Neustark spokesperson Elmar Vatter when I visited their facility in Berlin. Neustark is currently waiting for an approval according to the German emission control law (BImschG) for another facility in the western part of Germany since almost a year.
The most visible part of Neustark's plant is a large CO₂ storage tank. One to two times per week, around 20 tons of liquid CO₂ are shipped via truck from the biogas facility in Dresden to Neustark's plant in Berlin and pumped into that storage tank. The CO₂ liquefaction is one of the most energy-intensive steps in the chain, but it is necessary to make CO₂ transport practical.
In the plant, carbon dioxide is turned back into a gaseous state and then fed into metal casings where crushed concrete is essentially bathed in the greenhouse gas. This process takes between two and four hours.
What makes Cement so damaging makes Neustark's technology possible
Neustark's technology lets carbon dioxide react with calcium hydroxide. In essence, the technology does the opposite of what makes cement production so damaging to the climate. A key ingredient of cement and concrete is clinker, which is made by converting calcium carbonate (CaCO3) to calcium oxide (CaO), a reaction that produces plenty of carbon dioxide as an unwanted by-product. Before its use, cement is mixed with water. That water reacts with the calcium oxide in the clinker, producing calcium hydroxide.
That calcium hydroxide is what makes Neustark's technology possible: By letting it react with CO₂ and turning it back into calcium carbonate, carbon is permanently stored. This reaction also happens naturally in concrete with CO₂ from the air, but only at the surface and much slower.
"The strength of this approach is that it is permanent," says Valentin Gutknecht, one of Neustark's founders. "Carbon dioxide is mineralized, most likely for millions of years."
Liquefying CO₂, transporting it by truck, and other steps in the process chain obviously need energy, which in substantial parts still comes from fossil fuels today. However, according to Gutknecht, the emissions in the process chain are minor compared to the CO₂ they remove. They achieve an efficiency of 93 percent for their operations in Switzerland, meaning that per ton of CO₂ stored, around 70 kilograms of CO₂ are emitted. In Germany, it is slightly worse due to higher emissions of electricity and longer transport distances, but the company says they still achieve an efficiency in the range of 85 to 90 percent.
The carbon-enriched material is used in similar ways to how it would have been if it hadn't been processed by Neustark's process. In Germany, most of it is used as filling material in road construction. Not exactly a high-value use case and also not necessarily the best partner for the climate — Germany's traffic sector regularly fails to achieve any emission reduction targets.
A better use would be to use the material as aggregate in recycled concrete. It could reduce the amount of gravel needed. In this scenario, Neustark's technology has an additional advantage: The chemical composition of the carbon-enriched concrete allows reducing the amount of clinker in the concrete. Thereby, it reduces the need for the material that produces so much carbon dioxide in its production process.
Recycled concrete is already used regularly in Switzerland, which is often named as a positive example in this area. However, in Germany, hardly any concrete waste finds its way into recycled concrete due to regulatory barriers and a lack of supporting policies.
One of the larger players in the Carbon Removal Market
Neustark's facility in Marzahn can store around 1,000 tons of carbon dioxide per year. All of Neustark's current plants combined have a capacity of around 7,000 tons per year.
Is that significant? Certainly not if compared to existing emission sources. The city of Berlin emits around 16 million tons of carbon dioxide per year, so Neustark's plant hardly makes any difference. But as Valentin Gutknecht says, Neustark is already one of the larger players in the carbon removal market with that capacity.
Neustark's business model is to sell carbon removal certificates to entities that want to make up for their emissions. According to the carbon removal information website CDR.fyi, the bank UBS and the software company Microsoft are among Neustark's largest buyers.
Carbon compensation schemes and climate neutrality claims by companies based on certificates have come under increasing criticism in recent years. It is often highly questionable if certificates are related to any emission avoidance that would not have happened otherwise.
Carbon removal companies like Neustark position themselves as providers of more trustworthy certificates. Additionality is easier to validate, as it is relatively obvious that no one would actively remove CO₂ from the atmosphere without a business model. It is also highly unlikely that mineralized carbon will later escape into the atmosphere — a common concern about natural carbon sinks.
Neustark does not publicly communicate what its certificates cost and currently only targets businesses as its customers. According to CDR.fyi, carbon removal credits for mineralization technologies cost around 320 US dollars. This is a lot more than what less trustworthy certificate providers charge. Those are traded at prices between 4 and 8 US dollars. But it is still a lot less than what the company Climeworks — also from Switzerland — charges to remove CO₂ directly from the air via direct air capture.
Yet, ultimately, the voluntary carbon removal certificate market is only a means to develop technologies now that the world might need at much larger scales in the future.
Gutknecht says that by 2050, the world will need to remove around 10 billion tons of carbon dioxide annually. "This will need a completely new industry of the size of the current oil and gas sector," says Gutknecht. He estimates that carbon storage in construction waste and other mineral wastes like slags and ashes could provide around half a billion tons of this capacity.
Neustark's near-term goal is more modest: the company wants to develop the capacity for 100,000 tons of CO₂ removal per year by 2026 – and one million tons by 2030.
Author: Hanno Böck
I don't like paywalls, and I guess you don't like them either. You can read my articles for free, but researching and writing them takes time and effort.
If you enjoy reading this newsletter regularly, please consider supporting my work. You can donate to support my work via Patreon. If you work for a company or organization that may want to sponsor the newsletter or advertise in it, please get in touch.
If you do not want to support me financially, that is, of course, also fine. You can still help me tremendously by sharing this newsletter. If you found this text insightful, please forward it to others or share it on social media, in your organization's chat, or wherever you find appropriate.