Cement's future could be a combination of Carbon Capture and Electrification
Cement is an industry where capturing carbon emissions may be necessary. A combination with process heat electrification could be better than CCS alone.
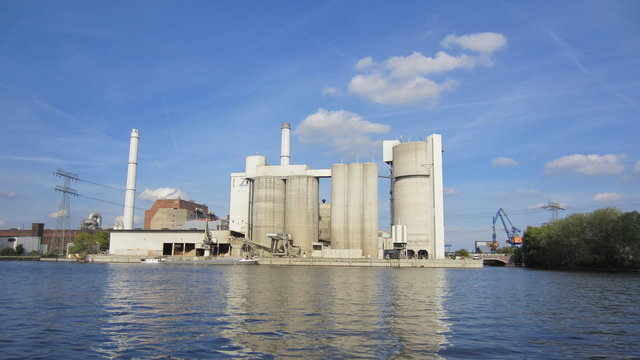
Cement is often named the prime example when discussing industries that are difficult to decarbonize. Cement production produces large amounts of carbon dioxide, and most of these emissions come from chemical reactions that cannot be avoided.
Cement is the material that gives concrete its strength and binds sand, gravel, and other input materials together, and cement's main component is called clinker. The production of clinker starts with a process called calcination. Calcium carbonate (CaCO₃) from limestone is heated to around 800 degree Celsius (~1500 °F), which converts it into calcium oxide (CaO).
This chemical reaction produces carbon dioxide as a by-product, and this is where most of the emissions come from. In a second step, the calcium oxide is heated to even hotter temperatures – around 1400 degree Celsius (~2600 °F) – in a process called sintering that gives cement its strength.
Around 30 percent of the emissions come from process heat for the calcination step and the sintering. Even though the sintering requires higher temperatures, more energy is needed for the calcination step. Today, process heat for cement production is usually provided by fossil fuels. A small share comes from burning waste or biomass.
The calcination emissions are what make cement production a unique decarbonization challenge. No other industry has such large amounts of emissions that do not come from fossil fuels. Even if clean energy would provide process heat, most of the emissions would still be there. Therefore, cement is often named as an industry that will require carbon capture and storage (CCS) - technology that captures carbon dioxide emissions and stores them in geological formations underground.
CCS has always been a controversial technology, with many critics seeing it as merely a tool by the fossil fuel industry to delay real climate action. Yet, in the debate, a key argument is that CCS will be required anyway for some industrial emissions – and cement is the prime example.
CCS for Cement should be less controversial than for Fossil Fuels
It would therefore appear that a cement plant with CCS would be much less controversial than other CCS projects. However, despite cement's key role in the CCS debate, not a single cement plant with CCS is operational today, and only one is under construction.
Despite its significant carbon footprint, the cement industry has been slow to adopt any significant decarbonization technologies. What's worse: According to the International Energy Agency (IEA), the emission intensity per ton of cement has increased between 2015 and 2021, primarily due to an increased share of clinker in the cement.
The Global Cement and Concrete Association, a lobby organization representing most of the cement industry, published a roadmap in 2020 with a commitment to net zero cement production by 2050. However, the industry does not appear to be in any hurry. According to the roadmap, the industry expects that by 2030, around ten cement plants with carbon capture and storage will be operational. There are around 4,000 cement plants worldwide.
I talked to Antoine Koen and Ingrid El Helou from the think tank Future Cleantech Architects (FCA), an organization looking at climate solutions for challenging sectors like cement and aviation. FCA has recently published a one-page fact sheet about cement decarbonization that provides a good summary.
According to Koen, one issue with cement is that the industry has low margins, and therefore it does not have a lot of capital for investments in research and development. Also, for obvious safety reasons, the use of cement is tightly regulated, and introducing changes is therefore often difficult and leads the industry to be conservative. Furthermore, the industry did not have a lot of incentives to reduce its emissions, though at least in the EU upcoming changes in the emission trading system will increase pressure.
Post-combustion CCS is expensive
Heidelberg Materials is currently building the first CCS facility at a cement plant in Brevik, Norway. Plans are to ship its emissions to Northern Lights, a carbon dioxide storage project that expects to receive emissions from industries all over Europe.
While a significant step forward, the project in Brevik comes with a caveat: Even with CCS, the plant will only capture around half of its emissions. Heidelberg Materials plans to have higher capture rates in a follow-up project in Slite, Sweden.
Capturing emissions needs significant amounts of energy in the form of process heat. Heidelberg Materials plans to utilize waste heat from the cement plant in Brevik for the capture process, but that limits the amount of carbon dioxide that can be captured.
Combustion processes, like in power plants, but also for cement process heat, create a mixture of gases, with the largest share being nitrogen. To capture carbon dioxide, it needs to be separated from nitrogen and other gases – and this process is energy intensive and expensive.
This expensive separation step, which uses a technology called amine scrubbing, is why most existing CCS projects are at processes that already produce exhaust streams of almost pure carbon dioxide (mainly fossil gas processing facilities).
While the Brevik CCS project will use amine scrubbing, other projects are looking at potential alternatives. Oxyfuel is a technology based on the idea that instead of operating combustion processes with ambient air, they can also operate with pure oxygen. The resulting exhaust gases would not contain nitrogen and will be largely composed of carbon dioxide and water vapor, which makes separation easier. However, oxyfuel CCS has only been used in small pilot plants yet. Thyssenkrupp is working on an improved oxyfuel process for cement plants.
Electrification of Process Heat would make CCS easier
As mentioned earlier, most of cement's emissions come from the calcination reaction. The calcination itself produces a relatively pure carbon dioxide stream. Therefore, the challenges just discussed are an issue of the combustion of fossil fuels to generate process heat.
With the trend towards cheaper renewable energy, electrifying process heat could be an interesting option. This would not only directly avoid around 30 percent of emissions but also make CCS for the remaining emissions easier due to the higher concentration of carbon dioxide. Furthermore, it would avoid any concerns about upstream emissions from fossil fuels. However, experience with electrifying very high-temperature processes is limited.
The finnish company Coolbrook is developing an electric high-temperature heat technology. It plans to apply it both to processes in the chemical industry (steam cracking) and to cement production. Its rotodynamic heater technology works by accelerating gases to supersonic velocities and then decelerating them, turning kinetic energy into heat.
Coolbrook has announced multiple partnerships with large cement companies. In a webinar, Coolbrook's CEO, Joonas Rauramo, explained that the company expects to develop its technology in multiple stages, with early projects only being used to power small parts of the cement production process. By 2025, Coolbrook expects to be able to power whole cement plants, and by 2030 it hopes to combine this with CCS technology.
Another company trying to electrify cement production with a different approach is SaltX from Sweden. Their process involves heating gas in an electric arc reactor (an electric arc is an artificial lightning) to temperatures that turn it into a plasma state. The plasma is used to provide process heat.
SaltX is currently testing its technology in collaboration with the quicklime producer SMA Mineral in a project called ZEQL (Zero Emission QuickLime). A pilot facility should be operational this year. The project hopes to have a full-scale quicklime plant running by 2025.
As Corey Blackman from SaltX explains to me, the quicklime industry is a good test case, as it is like a smaller version of the cement industry. Like cement, quicklime is produced from limestone and involves the same calcination reaction turning calcium carbonate into calcium oxide. However, it does not include sintering. Therefore, a quicklime plant is similar to the first step in a cement plant, just smaller.
Whether these technologies succeed remains to be seen. However, the combination of CCS with electrification appears to be one of the most promising options for the future of cement production.
Less Cement and completely new Processes
Some other paths toward lower cement emissions deserve to be mentioned. Any efforts to reduce the amount of cement used make the task easier. That can involve refurbishing old buildings instead of building new ones or just not building some things altogether.
Alternative building materials like wood and more efficient use of materials can reduce the amount of cement needed for construction projects. Different mixtures can reduce the amount of clinker needed in cement (see for example LC3).
On the other end of the spectrum are approaches that completely reinvent how cement is made, avoiding calcination altogether. A company called Novacem once tried to develop cement with a completely different chemical composition based on magnesium instead of calcium. However, a planned pilot plant was never built, and the company was liquidated in 2012.
Noteworthy startups that work on entirely new cement production processes include Brimstone Energy and Sublime Systems. By using different input materials or electrochemical processes, they aim to reinvent how cement is made. While an interesting space to watch, these technologies are very speculative.
Update: See also "How to make Cement without Carbon Emissions" on YouTube.
Author: Hanno Böck
I don't like paywalls, and I guess you don't like them either. You can read my articles for free, but researching and writing them takes time and effort.
If you enjoy reading this newsletter regularly, please consider supporting my work. You can donate to support my work via Patreon. If you work for a company or organization that may want to sponsor the newsletter or advertise in it, please get in touch.
If you do not want to support me financially, that is, of course, also fine. You can still help me tremendously by sharing this newsletter. If you found this text insightful, please forward it to others or share it on social media, in your organization's chat, or wherever you find appropriate.
Brief
-
Agora Energiewende has published a report about steel decarbonization and a coal phase-out in the steel industry. Agora expects that a fast decarbonization of the industry is possible and sees hydrogen-based DRI and increased use of scrap recycling as the leading technology to achieve this. Notably, Agora does not expect CCS to play a major role in steel decarbonization.
-
Hydrogen is considered a promising decarbonization option for some sectors. But even green hydrogen can be a climate problem - if it leaks into the atmosphere. New research puts its global warming potential over 100 years at around 11 (meaning 11 times as bad as CO₂). Not as bad as methane, but still substantial. Hydrogen infrastructure will need to be built with very low leakage rates.
-
Countries with a large potential for renewable energy could export that energy in the form of hydrogen. But transporting hydrogen, particularly by ship, is difficult and comes with substantial losses. Sanjeev Gupta, CEO of the steel and mining company GFG Alliance, thinks that exporting products made with hydrogen instead of hydrogen itself makes more sense.
-
Readers of my newsletter will be familiar with the issue of double counting green electricity from Iceland through guarantees of origin. In a recent press release, Iceland's largest electricity producer Landsvirkjun praises itself for its low emissions per kilowatt-hour. This is only true if one does not account for certificate sales, and noteworthy as Landsvirkjun had previously claimed that the issue of double counting is within the responsibility of its customer.