Making Glass without Fossil Gas
Today, glass production uses primarily fossil fuels and comes with substantial carbon emissions. Electrification could change that, but it probably cannot be scaled enough to power large production facilities completely. And even a glass industry powered by renewable energy would have remaining CO₂ emissions.
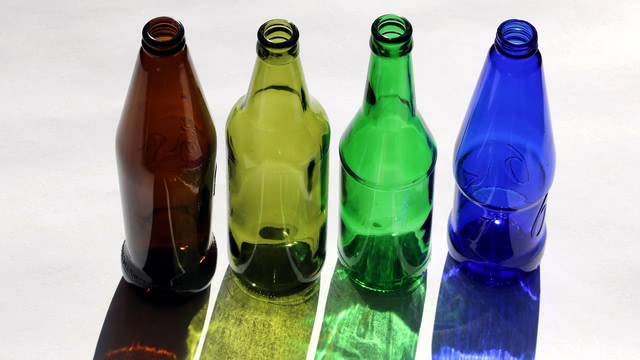
Carbon emissions from the glass industry do not get the same attention as the ones from larger industries like steel and cement. But with an estimated 95 million tons of carbon dioxide emissions, the glass industry is still a substantial contributor to climate change – and avoiding these emissions comes with considerable challenges.
Most of the energy in glass production is needed in the melting process. Melting glass requires high temperatures. Typical glass furnaces can reach temperatures of 1,600 degrees Celsius (around 3,000 degrees Fahrenheit). Today, the primary energy source for glass furnaces is fossil gas.
Glass furnaces usually run continuously for up to 15 years and cannot be stopped during operation. Therefore, changes in the production process can usually only happen during major revisions.
Until now, the glass industry relied on two strategies to reduce emissions: Efficiency improvements and increased recycling rates. While both can reduce the energy required, their potential is limited, and they do not provide a path towards climate neutrality.
Increased climate ambition and policies have lately created more pressure on the industry to develop new technologies to tackle its emission problems. Glass industry associations like the Bundesverband Glasindustrie in Germany or British Glass in the UK have published roadmaps that provide insights into the industry's plans and visions for a lower emission future.
Electrification considerably increases energy efficiency
One option to substantially decrease fossil fuel use and thus emissions is to electrify the heat supply. Fully electric glass furnaces already exist, but only at small scales. Molten glass is conductive, which means that one can run an electric current through the glass, which acts as a resistor and thus heats up.
Apart from other advantages like the ability to use renewable energy and the avoidance of air pollution, electrification can considerably increase the energy efficiency of glass production. The mentioned roadmap by the German glass industry mentions efficiency increases from 45 percent for a conventional, gas-fired furnace to 85 percent for a fully electric furnace.
One reason for these considerable increases in efficiency is unavoidable waste heat in conventional glass furnaces. As the UK glass industry report mentions, around a third of the energy supplied to a glass furnace ends up as heat in the exhaust fumes – despite waste heat recovery. It is a reminder that burning fossil fuels – or any other fuel – is often incredibly inefficient.
But an open question about fully electric furnaces is how much they can be scaled up. It is considered challenging to realize larger electric furnaces. Multiple people I talked to mentioned a failed attempt to build a large electric glass furnace in the United States.
A major accident destroyed an electrified furnace in 2008
In 2008, the company Cameron Glass started operating an electric furnace for wine bottles with energy provided by hydropower in Kalama near Portland, Oregon. Two months after the plant was started, it caused a leak of molten glass. The plant was destroyed and Cameron Glass eventually filed for bankruptcy.
"That was a real trauma for our industry," said Fabrice Rivet from the European Container Glass Federation (FEVE), whom I interviewed last year. It likely hampered any interest in the glass industry for further electrification projects.
Today, the industry expects that fully electric furnaces will only be feasible up to a certain size. An alternative are hybrid furnaces that use mostly electricity and some gas. Eventually, they could be converted to green hydrogen, leading to a fully decarbonized energy supply.
Hybrid furnaces already exist. Many larger glass furnaces have electric boosters that provide between 10 and 20 percent of the heat energy. Future hybrid furnaces could operate with much higher electric shares.
The industry association FEVE had plans to kickstart the technology for such a hybrid furnace as a collaborative project from different glass manufacturers, the Furnace for the Future. Plans were to build an 80 percent electrified furnace for container glass. However, the project failed to get funding from the EU Innovation Fund.
Hybrid furnaces will be built in Germany and Czechia
But while the project was not realized under the umbrella of FEVE, it will eventually be built in a different setting. Ardagh, the company supposed to host the Furnace of the Future at one of its sites in Germany, received funding from a German government program to support industrial decarbonization. It will now be built under the name Next-Gen Furnace. Furthermore, the Glassmaker Schott received funding for multiple electrification projects producing special glasses from the same funding program.
In the latest round of the EU Innovation Fund, a project in Czechia by AGC Glass Europe called Volta received funding for constructing and operating a flat glass furnace with up to 75% electrification.
These hybrid furnaces will still use fossil gas for some of their energy needs. Renewable gases like green hydrogen or biomethane could replace this gas. It would also be possible to run furnaces entirely on biomethane or hydrogen, and investment costs would be lower as it would require little or no changes to existing technologies. But it appears unlikely that this will happen at meaningful scales.
The availability of biomethane and other bioenergy sources will probably remain limited. With green hydrogen, the efficiency problems of gas furnaces are exacerbated. In addition to the burning process's losses, producing hydrogen with clean electricity and electrolyzers also involves energy losses. Furthermore, burning hydrogen can increase air pollution due to the generation of more NOx emissions. Exhaust gas treatment can avoid NOx emissions, but that increases energy needs again.
Therefore, it appears that the industry should electrify as much as possible and use hydrogen or bioenergy sources only in small quantities. This is also reflected in the roadmap of the German glass industry. It provides three possible scenarios: Two extreme scenarios that either favor electrification or hydrogen and a third hybrid scenario where they selected what they expected to be the most economically viable option for each glass production site.
In the most likely hybrid scenario, the amount of electric energy used is only slightly less (30 Petajoule electricity per year, 9 Petajoule hydrogen) than in the extreme electrification scenario (31 Petajoule per year, 3 Petajoule hydrogen).
It is interesting to consider this in the context of the bigger picture of hydrogen use in industries. High-temperature heat is often named as one of the areas where hydrogen might be a good option. The glass industry operates at very high temperatures, and electrification technologies likely have limitations. Still, hydrogen will probably play a minor role and the bulk of the energy will be provided by direct electrification.
With a combination of fully electric and hybrid furnaces, the glass industry can avoid its energy-related carbon emissions. Of course, that also requires sufficient renewable electricity and the corresponding infrastructure. The latter should not be underestimated. According to the German glass industry roadmap, providing the necessary grid connections for the massively increased electricity requirements can take several years.
An unsolved problem: Process emissions from carbonates
Emissions from burning gas are not the only emissions in the production of glass – there are also carbon emissions from the raw materials. The three main ingredients for typical types of glass are silica (silicon oxide), soda (sodium carbonate), and limestone (calcium carbonate). The latter two, as their chemical name suggests, contain carbon.
In the glassmaking process, sodium carbonate is converted into sodium oxide and calcium carbonate into calcium oxide. A by-product of that chemical reaction is carbon dioxide. These process emissions are responsible for around a fourth of the glass industry's emissions.
One way to reduce these process emissions is to increase the recycling rates. Recycling rates differ widely depending on location and glass type. More than 80 percent of container glass in Europe is already recycled, so there is limited potential for improvement. In the United States, it is only about a third.
Flat glass used in construction is recycled much less than container glass. Most of it ends up in landfills, and the rest is usually mixed as an aggregate into other materials and not recycled into new glass. British Glass expects that this could be changed.
"The majority of end-of-life glazing in buildings could be dismantled and recycled," the organization writes in its roadmap, "however, contamination is the main barrier to recycling flat glass."
While increased recycling rates can decrease process emissions, they cannot entirely avoid them. The glass industry could also use alternative input materials, but research on this is in the early stages.
The German glass industry roadmap mentions that some glass manufacturers have used a by-product from chlorine production, sodium hydroxide, as a replacement for soda. Research projects have also tried using other industries' ashes as supplemental materials.
It seems unlikely that these efforts will solve the process emission problem completely. Another option would be to use carbon capture and storage (CCS). However, CCS in the glass industry is currently completely untested, and it is unclear what challenges that would entail. The roadmap from British Glass says about CCS: "Viability of capturing CO₂ from the furnace waste gas still needs to be demonstrated. The current amine scrubber technologies are not compatible with glass furnace flue gases."
Fabrice Rivet from the container glass federation FEVE is skeptical that the glass industry will use CCS due to the high infrastructure costs for CO₂ pipelines.
While electrification can probably solve most of the glass industry's carbon emission problem, it will not solve it completely. It is still an open question how the glass industry can become compatible with a climate-neutral future.
Author: Hanno Böck
I don't like paywalls, and I guess you don't like them either. You can read my articles for free, but researching and writing them takes time and effort.
If you enjoy reading this newsletter regularly, please consider supporting my work. You can donate to support my work via Patreon. If you work for a company or organization that may want to sponsor the newsletter or advertise in it, please get in touch.
If you do not want to support me financially, that is, of course, also fine. You can still help me tremendously by sharing this newsletter. If you found this text insightful, please forward it to others or share it on social media, in your organization's chat, or wherever you find appropriate.
Brief
-
Advanced geothermal technologies are gaining traction: Eavor, which has developed a closed-loop geothermal system, has signed a heat supply contract with the city of Hannover, Germany.
-
The Netherlands stopped gas extraction at the Groningen gas field. A rare example of a country voluntarily deciding not to use fossil fuel resources. Gas drilling in Groningen was controversial due to earthquakes and building damages.
-
Remember Haru Oni, the e-fuel plant in Chile? The company behind it, HIF, has now announced that it has submitted an environmental permit for a larger follow-up project called Cabo Negro. As I already suspected, HIF will focus on producing e-methanol - although HIF notes that it theoretically could convert that e-methanol into e-gasoline.
Articles elsewhere I found worth reading:
-
"Climate change demands that we achieve both growth and degrowth, depending on the activity and economic sector in question," writes economist Gernot Wagner.
-
Free public transit is a popular demand by some climate activists for the decarbonization of transport. But is it working? Experiences and numbers from Tallinn, Estonia, indicate that it is not.