BASF starts the World's First Electric Cracker Furnace
Electrifying steam cracking can reduce emissions in the chemical industry, but it does not change the use of fossil input materials. It is only a first step towards climate-neutral chemicals.
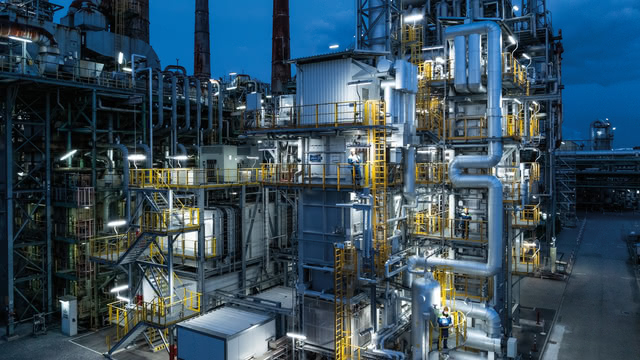
The chemical companies BASF, SABIC, and Linde have announced the startup of the world's first large-scale electric steam cracking furnace at BASF's site in Ludwigshafen, Germany. Steam crackers are amongst the most important and energy-intensive facilities in the chemical industry.
Steam crackers convert fossil input materials into basic building blocks of many products. In Europe, most steam crackers process naphtha made from oil. Elsewhere, using by-products from fossil gas drilling like ethane is also common. The most important output products of steam cracking are the olefins ethylene and propylene, which are the building blocks of most plastics.
The input materials in the cracker need to be heated to temperatures above 800 degrees Celsius (approximately 1,500 °F). Today, that heat is usually produced with fossil gas.
Two electric furnaces, six megawatts
BASF is now testing two electric furnaces, each with three megawatts electric power. Both use resistance heating, which is one of the simplest ways to turn electric energy into heat. One furnace directly heats the cracker, while the other uses radiative heat transfer.
Compared to some other industrial high-temperature processes, the temperatures in crackers are not exceptionally high. But, as BASF's Andrea Haunert explained to me in an interview I did in 2022 for a previous article, the chemical reaction inside the cracker is endothermic. That means the reaction itself consumes energy that must be constantly provided.
While BASF says it is testing the technology at an industrial scale, the electric furnaces are still small compared to the gas-powered ones BASF operates.
BASF spokesperson Thomas Nonnast told me that the existing Cracker 2 — the larger one of two steam crackers in Ludwigshafen — has ten furnaces that can each process around 20 tons of input material per hour. The two electric furnaces have a capacity of 2 tons per hour.
The project received around 15 million Euros in funding via a support program for the decarbonization of industries by the German government. According to the funding program, the total project costs are around 79 million Euros. BASF had previously tried to get funding via the EU Innovation Fund, but the electric cracker furnace was not among the selected projects.
Electric energy, but still a fossil feedstock
Electrification of chemical processes allows using renewable energy and can also increase energy efficiency due to avoided losses through hot emissions. However, it is important to realize that electric crackers do not enable a climate-neutral and fossil-free production of chemicals.
The chemical industry uses fossil fuels not just as an energy source but also as its feedstock. Olefins and many other precursors of everyday products are made from fossil fuels, and electric crackers do not change that.
Carbon embodied in products like plastics usually ends up in the atmosphere in one way or another. It is most obvious in places like Germany, where most plastic waste ends up in waste incinerators. Emissions from those waste-to-energy plants are releasing carbon dioxide created by the fossil fuels that the chemical industry uses as inputs.
A truly climate-neutral chemical industry needs to replace its input materials. There are three options for this: biomass, recycled materials, and carbon capture and utilization technologies (CCU) that make carbon-containing chemicals from CO2 and hydrogen.
Two very different CCU approaches exist to make olefins and other cracker products. One involves making naphtha from a Fischer-Tropsch process and using that in steam crackers. An entirely different process can use methanol as its input material. It is already commonly used in China, although not for climate reasons: Methanol is made from coal gasification, which is very emission-intensive.
As we have discussed previously in this newsletter, the methanol-based CCU route has some efficiency advantages. While steam crackers may still be needed, it is not clear how big the role of the e-cracker will be in a future climate-neutral chemical industry.
Other companies have also announced plans for e-crackers
Other chemical companies have also announced electric cracker projects in recent years. For some of them, it is unclear whether they are still pursued.
Dow and Shell have received funding from the Dutch government for the development of an electric cracker. They announced the startup of a small, experimental unit in 2022 but have not made any further announcements since then. Dow and Shell have not answered questions about the state of the project.
More recently, Technip Energies, LyondellBasell, and Chevron have announced plans for an electric cracker at LyondellBasell's facility in Texas, USA.
An industry collaboration called "Cracker of the Future" led by the Chemelot chemical site in the Netherlands, also planned to develop an electric cracker. In 2021, the consortium announced that the companies Repsol and Versalis (Eni) joined the project. That was the last update from the project. Chemelot has also not answered questions about the project's status.
BASF and SABIC were originally part of the "Cracker of the Future" consortium. They left it to pursue their own project - which resulted in the two electric cracker units in Ludwigshafen.
Author: Hanno Böck
I don't like paywalls, and I guess you don't like them either. You can read my articles for free, but researching and writing them takes time and effort.
If you enjoy reading this newsletter regularly, please consider supporting my work. You can donate to support my work via Patreon. If you work for a company or organization that may want to sponsor the newsletter or advertise in it, please get in touch.
If you do not want to support me financially, that is, of course, also fine. You can still help me tremendously by sharing this newsletter. If you found this text insightful, please forward it to others or share it on social media, in your organization's chat, or wherever you find appropriate.
Brief
-
Two think tanks - IEEFA and Agora Industry - have recently published reports about the decarbonization of the steel industry. They share a common conclusion: Carbon capture technology is unlikely to play a significant role in emission reduction in the steel industry. Only one Steel-CCS project exists worldwide, which IEEFA's report discusses in depth. The Al Reyadah project in the United Arab Emirates is a gas-powered DRI plant that uses some of its CO2 for Enhanced Oil Recovery. According to IEEFA, capture rates are only around 20 percent. Most existing steel plants are coal-powered. Coal-fired blast furnaces with CCS technology currently do not exist at all.
-
Carbon Recycling International, the Icelandic company that pioneered CO2-to-methanol technology more than a decade ago, has announced a third large project deploying their tech in China.
-
The German environmental NGO Deutsche Umwelthilfe and the city of Borkum have won a court case in the Netherlands, stopping a gas drilling operation in the North Sea.