The path to Green Steel could be Hydrogen
Several steelmakers are investing in technologies that could clean up one of the biggest contributors to climate change.
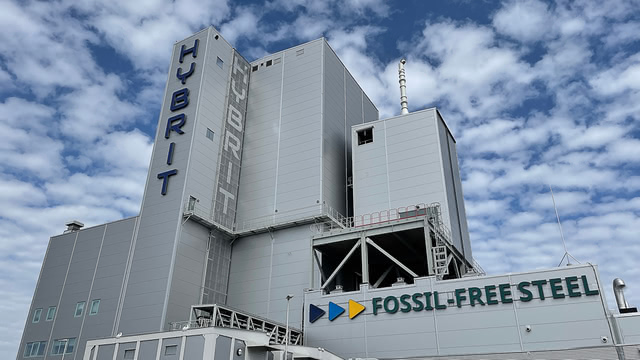
The steel industry is a major contributor to a heating climate. Around seven percent of worldwide carbon emissions come from steel factories. If indirect emissions like the electricity generation are included then it adds up to twelve percent.
So decarbonizing the steel industry is crucial. But changing the steel industry is not straightforward. It requires introducing new technologies to replace the coal responsible for most of the steel industry's large carbon footprint. Last year, the Swedish steel producer SSAB announced the first shipment of fossil-free steel, produced with hydrogen in a small pilot facility.
Steelmaking starts with mining iron ore. Iron is not contained in pure form, but in the form of iron oxide. This means that the iron atoms are chemically bound to oxygen atoms, and this bond needs to be broken in the steelmaking process.
Coke is used as a chemical reduction agent
The most common method is to use coke in a blast furnace. Coke is essentially coal where the carbon content has been enriched. This process of producing coke already creates sizable emissions. In a coke plant, around a fifth of the carbon content of the original coal ends up as carbon dioxide.
Coke is then used to turn the iron ore into pure iron. This is done in a blast furnace, where most emissions are created. The result is melted iron, which is then further processed in what is called a basic oxygen furnace.
It is crucial to understand coal's role in steelmaking: It is not merely used as an energy source. Instead, the carbon in the coal is used as a chemical agent required to run the process of turning iron oxide into pure iron.
A different path to steelmaking is to recycle steel scrap. Steel scrap can be melted in an electric arc furnace. These already run with electricity. Therefore, recycling steel can be largely emission-free if the electricity comes from clean sources.
Using steel scrap avoids the carbon-intensive process in the blast furnace, and steel can be recycled indefinitely without quality loss. However, most steel is already recycled, and while increasing recycling rates is desirable, the amount of steel scrap that can be collected is ultimately limited. Therefore, cleaner production methods for new steel are needed.
Direct reduction with hydrogen can replace the blast furnace
Apart from the blast furnace operated with coal, there is another way to make steel using fossil gas. This process is called direct reduction and is already an established technology. Direct reduction produces something called sponge iron, which can be melted in an electric arc furnace - the same technology used for scrap steel.
Instead of coke made from coal, fossil gas acts as a chemical reduction agent. While this process has lower emissions than the blast furnace, it is still based on fossil fuels, and the emissions are still significant.
But direct reduction can be changed to run on hydrogen. And hydrogen can, at least in principle, be made with electricity. If the electricity source is green, then direct reduction with hydrogen has very few emissions left. That is the path the Swedish steelmaker SSAB wants to take, and several other steel companies have since announced similar plans.
In principle, the technology works: SSAB has built a pilot direct reduction plant with hydrogen in the city of Luleå in northern Sweden. It delivered the sponge iron for their first fossil-free steel shipment. SSAB plans to open a larger demonstration plant and hopes to be able to deliver steel in industrial quantities by the year 2026.
While SSAB was the first company to have a hydrogen-based direct reduction plant operational, they are not the only one betting on this technology. In the Swedish town Boden, not far from SSAB's pilot plant, a consortium of investors named H2 Green Steel also plans to build a hydrogen-based steel facility.
German company Salzgitter plans to produce its first hydrogen-based steel in 2025 and wants to complete its transition away from all coal-based blast furnaces by 2033. Other steel companies have made similar announcements, though few with a timeline as ambitious as the one by Salzgitter.
An advantage of hydrogen-based direct reduction is that most of the technology is already known. The industry has experience with direct reduction. Around five percent of today's steel production uses direct reduction with fossil gas.
Fossil gas also allows for an intermediate step: Steel companies could build direct reduction facilities that they operate with fossil gas for an intermediate period and switch to hydrogen later. However, the current increase in fossil gas prices does not make that intermediate option easier.
Huge amounts of hydrogen needed
The biggest challenge for hydrogen-based steel is the production of the massive amounts of hydrogen necessary for the process. Hydrogen is often hailed as a promising climate solution. But today most hydrogen is produced from fossil fuels, usually gas.
Using hydrogen from fossil gas to power a steel plant would not make much sense. That would cause more emissions than using fossil gas directly.
Hydrogen can be produced by splitting water with electricity in a process called electrolysis. If the electricity is made from renewables, then this process has no direct carbon emissions. Hydrogen produced this way is often called green hydrogen.
Other ways are discussed to make cleaner hydrogen, particularly combining fossil-based hydrogen production with carbon capture technology. However, this so-called blue hydrogen is more controversial - the emissions produced depend on leakage rates both for the fossil gas and for the carbon capture process. So using primarily green hydrogen would be preferable.
Today, few green hydrogen production facilities exist, and the economics are challenging. Many companies are currently investing in hydrogen production capacities, and hopes are that green hydrogen will become much cheaper in the coming years through technology improvement.
But at least today, even if steel companies manage to source enough green hydrogen, producing green steel will cost more. That means either customers need to be willing to pay a premium for a green product, or there need to be public subsidies. SSAB's project is currently supported by the EU Innovation Fund, a major funding program by the European Union for climate-friendly industry projects.
Obviously, the economics of green steel could improve if green hydrogen gets cheaper or if policy changes regulate carbon dioxide emissions or make them more expensive.
But if climate goals are taken seriously, the steel industry needs to act quickly. The German think tank Agora Industry published an analysis last year that highlights the need for a quick transformation.
According to Agora, around 70 percent of global blast furnace capacities will require major reinvestment before 2030. Since blast furnaces operate for many decades, new investments in coal-based steel production can cause a lock-in to fossil fuel capacities that cannot operate for their full lifetime if climate goals are enforced. Agora concludes: "The global steel transformation needs to start in the 2020s. Key low carbon technologies are ready and can be deployed now."
Author: Hanno Böck
I don't like paywalls, and I guess you don't like them either. You can read my articles for free, but researching and writing them takes time and effort.
If you enjoy reading this newsletter regularly, please consider supporting my work. You can donate to support my work via Patreon. If you work for a company or organization that may want to sponsor the newsletter or advertise in it, please get in touch.
If you do not want to support me financially, that is, of course, also fine. You can still help me tremendously by sharing this newsletter. If you found this text insightful, please forward it to others or share it on social media, in your organization's chat, or wherever you find appropriate.
Brief
- Glass manufacturer Verallia announced a partnership with the industrial engineering company Fives to build an all-electric glass melting furnace in Cognac, France.
- DemoUpCARMA, a research project by ETH Zürich around carbon capture technologies, announced a first shipment of carbon dioxide via containers to Iceland.
- SSAB, the Swedish steel company mentioned in the main article, announced that an underground hydrogen storage facility in Luleå is now in operation.
- The United States have approved the ratification of the Kigali Amendment, to the Montreal Protoocl. The Kigali Amendment is an international effort to reduce the use of hydrofluorcarbons (HFCs), which are extremely potent greenhouse gases.