Reducing Glass Industry Emissions with Sodium Hydroxide
Glass production generates process emissions that cannot be avoided by switching to renewable energy. A circular carbon process to make soda ash, an essential raw material for glass production, could help tackle those emissions, but it comes with some caveats.
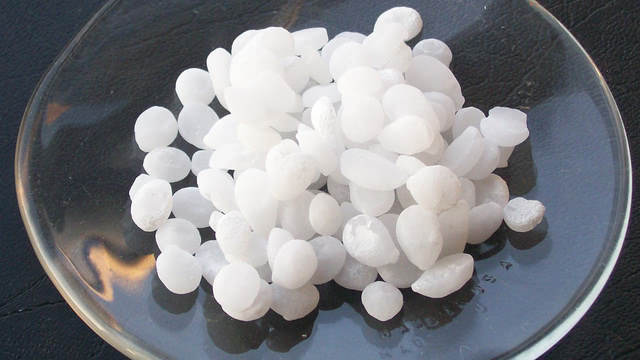
The production of glass is an emission-intensive process. For each ton of glass that ends up in windows and bottles, around 0.7 tons of carbon dioxide are released into the atmosphere.
The bulk of emissions in the glass industry are the result of burning fossil fuels like oil or gas to melt the input materials that eventually form glass. The obvious solution is to switch to clean energy sources. Most of the energy in glass furnaces could be electrified, although, as discussed here previously, full electrification is challenging and may be infeasible. Still, the bulk of emissions in the glass industry could be avoided by electrifying most of its energy and potentially using small amounts of green hydrogen for large furnaces that cannot be fully electrified.
Since my latest newsletter on the topic, glass producers have made progress with electrification. French glass maker Verallia inaugurated the currently largest fully electric glass furnace in September this year. Since late 2023, the company Ardagh has operated its hybrid, mostly electric Next-Gen furnace in Germany. While still using some fossil gas, Ardagh reports emission reductions of 63 percent.
However, even furnaces fully powered by clean energy have remaining carbon dioxide emissions. These are the result of chemical reactions within the furnace. The production of glass involves three major ingredients: Silicon dioxide, sodium carbonate - also called soda ash or simply soda - and calcium carbonate. The latter two are a problem.
Chemical decomposition causes one-fifth of the glass industry's emissions
When exposed to the heat of a furnace, a chemical reaction releases carbon from those input materials. Sodium carbonate with a chemical formula of Na₂CO₃ becomes sodium oxide (NaO). Calcium carbonate (CaCO₃) gets turned into calcium oxide (CaO). The latter is the same chemical reaction that makes cement production so damaging to the climate.
The European Container Glass Federation (FEVE) recently published a decarbonization report and addressed these questions: "While 80% of direct greenhouse gas emissions in container glass production come from combustion of natural gas to melt glass, the other 20% of direct CO₂ emissions are process emissions arising from the decomposition of carbonates during the melting of the virgin raw materials required to make new glass. These emissions can be significantly reduced if virgin resources are replaced with recycled content, in particular recycled glass (or cullet), or with alternative low carbon raw materials."
As FEVE indicates, the industry association sees increased recycling rates as one way to tackle those residual emissions. That is valuable and has other benefits, but it will probably not be possible to establish a perfect, fully circular recycling system.
FEVE refers to the possibility of alternative raw materials and, later in the report, mentions that Verallia, the French glass company pioneering electric glass making, has been experimenting with alternative inputs. Verallia has only published very limited information about these efforts, but it mentions approval of an alternative calcium source in its 2023 sustainability report and announces: "It will be deployed in plants on a large scale in 2024." (Verallia has not answered to questions for this article.)
I was recently contacted by the company Capital Gain Consultants. The consulting company has a proposal on how to tackle some of these process emissions of the glass industry. Capital Gain Consultants offers to perform feasibility studies with their own simulation software.
Instead of sourcing soda ash externally, glassmakers could use their own carbon dioxide emissions to produce it. This process requires sodium hydroxide (NaOH), a solid chemical known as caustic soda, which is usually produced as a by-product of chlorine production.
The idea seems appealing. Regular readers of this newsletter will be familiar with the idea of carbon capture and utilization (CCU) - i.e., the idea of using CO₂ emissions to produce other chemicals or fuels - but this one has some key differences from the CCU processes we usually talk about.
Most ideas for CCU involve making energy-rich chemicals like methanol. Inevitably, turning low-energy CO₂ into something like methanol requires enormous amounts of energy, usually delivered in the form of hydrogen. This CCU process for soda ash is different. It does not require external energy, as it is an exothermic reaction.
Most carbon capture processes - whether for storage or further use - require a highly concentrated CO₂ stream. That is a major challenge, as flue gases often contain mostly nitrogen and only low concentrations of CO₂. In order to separate those gases, an absorbent material that binds CO₂ is needed. The commonly used method is amine washing, but this process is energy-intensive and expensive.
In the proposed carbon capture to soda ash process, sodium hydroxide itself acts as an absorbent and binds carbon dioxide. A separate separation process, like amine washing, is not required.
It is a carbon capture and utilization process. However, it skips the usually challenging part of carbon capture (CO₂ separation) and avoids the high energy requirements of other CO₂ utilization methods. It looks appealing, but there are some caveats.
While researching this article, I learned about another company pursuing a carbon utilization process to make soda ash. In 2016, Carbon Clean, a company headquartered in the UK, announced the launch of a pilot plant utilizing emissions from a coal power station in India. However, the announcement contains very little detail and does not mention what input material the plant is using. It may be an entirely different process. Carbon Clean has not answered to questions for this article.
Moving emissions to another facility is no solution
Like with any CCU process, it is worth looking exactly at what is happening to the carbon. As discussed previously, a naive look at CCU technologies can lead to an overestimation of emission savings.
Looking at the emissions from a glass furnace, we have different types of carbon dioxide sources. Given that existing furnaces are still overwhelmingly powered by fossil gas, there are CO₂ emissions of fossil origin. Furthermore, there are emissions from soda ash, calcium carbonate, and - in small quantities - other input materials.
If we only consider the emissions from decomposing soda ash, utilizing them to make new soda ash would create a circular process. While CO₂ would be created, it would be kept within the process. Such a process will likely never be perfect, so there will be residual CO₂ losses that would need some compensation in the form of an additional CO₂ source. (Such circular carbon or carbon cycling processes are generally an interesting idea. I previously covered a proposal for carbon cycling using methanol as an energy storage solution.)
But the soda ash proposal from Capital Gain Consultants goes a step further. It proposes that glassmakers could utilize additional CO₂ emissions to make excess soda ash that could be sold ("Generate revenue by selling excess Soda Ash"). Here, things get tricky.
If one glass producer captures its emissions to make soda ash and sells it off to another glass producer, those CO₂ emissions are not avoided. They are merely delayed. There would still be emission savings, but it is incompatible with a fully climate-neutral glass industry. In the long run, this is not a viable solution. However, a circular solution for soda ash emissions alone would already be attractive, yet it would require other solutions for the remaining emissions.
Upcoming regulatory changes for Soda Ash in Europe's Emission Trading System
Another question that glass companies looking into this carbon capture to soda ash process should consider is the regulatory framework. Glass factories operating in the European Union are covered by its Emission Trading System (ETS). It requires that industries generating carbon dioxide emissions need to invalidate emission certificates. These certificates can be traded and bought. However, in many cases, companies receive them for free to protect them from international competition. However, according to the EU's plans, this free allocation of certificates will eventually end and be replaced with the so-called carbon border adjustment mechanism (CBAM).
Yet, the relevant question here is whether a company using a carbon capture and utilization process can avoid using emission certificates. Perhaps surprisingly, the ETS does not just cover emissions released into the atmosphere. In many cases, just creating CO₂ already puts a process under the ETS. Whether that is the case often depends on industry-specific regulation.
Most soda ash today is produced using the Solvay process. A smaller amount is directly mined. The Solvay process utilizes sodium chloride (also known as table salt) and calcium carbonate. In the process, carbon is released from calcium carbonate and later bound in soda ash.
Notably, this process also involves the temporary creation of carbon dioxide. Under the current EU regulation, the soda ash producer is not responsible for this temporary carbon dioxide under the ETS. It is the responsibility of the glassmaker to account for these emissions.
However, this is about to change. The new regulation that will apply starting in 2025 says: "Intermediary CO₂ for the production of soda ash shall be considered as emitted by the installation producing the CO₂". (There is an exception for carbon permanently stored in building materials, but it does not apply here.)
As Fabrice Rivet from the glass industry association FEVE explained to me. "it is now the soda ash producers who will have to surrender allowances for the CO₂ in the soda ash, while the glass producers will no longer have to do it". An exception, however, would be imported soda ash produced in facilities not covered by the ETS.
This was also confirmed to me by a spokesperson of the European Commission. "To avoid double counting, the downstream glass production installation, as long as it is also an ETS installation, does not need to report and surrender emission allowances for the CO₂ emissions corresponding to the sodium carbonate used as an input (if purchased from an ETS soda ash producer) in the glass production process."
While these regulations were likely written with the traditional Solvay process in mind, they would apply to any alternative soda ash production process as well. If a glassmaker is using carbon dioxide emissions to make and sell soda ash, it would still be responsible for those emissions.
When asked about how these would apply to a circular process, the European Commission answered: "Regarding a circular process utilising CO₂ from the glass furnace itself, this implies that the installation is the producer and the consumer at the same time. The provisions described above for the production of soda ash would apply to the glass manufacturer at the start of the cycle when the emissions are derived from virgin materials. Subsequent capture and re-use of CO₂ would benefit from the provisions to avoid the double counting."
Based on these statements, it seems that a glassmaker utilizing a circular carbon soda ash production process could benefit by avoiding the need for emission certificates. There would, however, still be a need for emission certificates if soda ash is sold to other consumers.
The European Commission informed me that they plan to publish an updated guidance document with further details on the implementation of this new regulation soon.
It might be worth asking whether it is even necessary to convert sodium hydroxide into soda ash or whether it could be used directly in glass furnaces. A study published by the German glass industry organization BV Glass mentions that sodium hydroxide has sporadically been used as a soda ash replacement, but unfortunately, it contains no further details. BV Glass did not reply to questions for this article.
Dealing with process changes is always challenging, so the idea of having a decarbonization option that needs no process changes might still be appealing. However, whether sodium hydroxide is used directly or first converted into soda ash, sufficient amounts of sodium hydroxide are required in both cases.
Is there enough sodium hydroxide?
Sodium hydroxide is produced in the chloralkali process, in which a solution of sodium chloride is converted into sodium hydroxide, chlorine, and hydrogen. The process is very energy-intensive. However, with a clean electricity grid, chloralkali electrolysis produces no significant carbon dioxide emissions. (There can, however, be hydrogen emissions, and hydrogen is an indirect and largely unregulated greenhouse gas.)
Due to the nature of this process, chlorine and sodium hydroxide are always produced in a fixed ratio. It is not possible to increase the production of sodium hydroxide in the chloralkali process without increasing the production of chlorine. There needs to be a balanced offtake of those two products.
The world's glass industry consumes around 40 million tons of soda ash. Sodium hydroxide has a slightly lower weight per amount of sodium. Replacing all of the glass industry's soda ash would create an additional demand of over 30 million tons of sodium hydroxide. With a world market of around 80 million tons of sodium hydroxide today, it is easy to see that such a process applied at significant scales would put the chlorine and sodium hydroxide market out of balance, significantly increasing prices for sodium hydroxide.
Chlorine is a toxic gas. Disposing or neutralizing large quantities of it is likely not feasible. Furthermore, it is worth mentioning that chlorine chemistry is itself a controversial issue. The main product made from chlorine is polyvinyl chloride (PVC), a common type of plastic.
Burning PVC can create toxic gases. Some environmental organizations are campaigning for a ban or at least a restriction on PVC use. While it is not something on the immediate political agenda, with increasing discussions about the negative effects of plastics, there is a possibility that the production of PVC and other chlorine-based products will be restricted in the future. This would inevitably lead to a reduction in chlorine and sodium hydroxide production. For any process utilizing sodium hydroxide, this is a risk to be considered.
An alternative production process for sodium hydroxide called caustification is of no help either because it starts itself with soda ash and calcium hydroxide. Turning soda ash into sodium hydroxide in order to make soda ash is obviously not a great idea. This process also requires calcium hydroxide made from lime. Lime production has itself a process emission problem, as it involves converting calcium carbonate (CaCO₃) to calcium oxide (CaO), inevitably creating CO₂.
Alternative sodium hydroxide production methods are explored. Evonik is working on producing sodium hydroxide and sulfuric acid from salts in chemical wastewater using a method called electrodialysis. However, Evonik does not expect this method to be available anytime soon: "A standard process for the chemical industry is still a long way off."
Sourcing sodium hydroxide is probably the main challenge for the proposed carbon capture to soda ash process. While the idea might initially look appealing, it inevitably relies on generating sufficient amounts of sodium hydroxide in a viable way that does not create more emissions elsewhere. It is doubtful whether that is possible.
I received valuable feedback for this article from Peter Ruschhaupt (Future Cleantech Architects), Allanah Paul (Bellona), Ulrich Seifert (Fraunhofer UMSICHT), Adeline Farrelly and Fabrice Rivet (FEVE), and Armin Fricke (Capital Gain Consultants).
Update (2025-01-07): After publishing this article, I learned about another effort to make soda ash from chlorine by-products. The CODA research project, which involves the Max Planck Institute for Dynamics of Complex Technical Systems (Magdeburg, Germany) and CIECH Soda as partners, wants to build a pilot plant for such a process.
Author: Hanno Böck
I don't like paywalls, and I guess you don't like them either. You can read my articles for free, but researching and writing them takes time and effort.
If you enjoy reading this newsletter regularly, please consider supporting my work. You can donate to support my work via Patreon. If you work for a company or organization that may want to sponsor the newsletter or advertise in it, please get in touch.
If you do not want to support me financially, that is, of course, also fine. You can still help me tremendously by sharing this newsletter. If you found this text insightful, please forward it to others or share it on social media, in your organization's chat, or wherever you find appropriate.